Preparation method of lubricant
A lubricant and emulsifier technology, applied in the field of lubricant preparation, can solve the problems of inability to meet lubricant requirements, low reaction efficiency, and high energy consumption, and achieve the effects of increasing surface area, increasing reaction rate, and simplifying process
- Summary
- Abstract
- Description
- Claims
- Application Information
AI Technical Summary
Problems solved by technology
Method used
Examples
preparation example Construction
[0020] A preparation method of lubricant, comprising the steps of:
[0021] S1. Heat the base oil. When the oil temperature reaches 80-100°C, add stearic acid and an emulsifier with an HLB value of <6 and mix evenly to obtain an oil phase for later use;
[0022] S2. Mix water and polyhydric alcohol evenly to obtain water phase A. After fully stirring, slowly add water phase A to the oil phase and continue stirring for emulsification to obtain emulsion a for later use;
[0023] S3. Mix the polyol, the emulsifier with an HLB value>15, and water evenly to obtain an aqueous phase B, add the emulsion a obtained in step 2 into the aqueous phase B under stirring, and continue to stir for emulsification to obtain an emulsion b, which is set aside;
[0024] S4. Potassium hydroxide is mixed with water to obtain a potassium hydroxide solution; then the emulsion b obtained in step 3 is added to the potassium hydroxide solution under stirring for saponification reaction to obtain a soap-ba...
Embodiment 1
[0028] First heat the base oil, when the oil temperature reaches 80-100°C, add stearic acid and an emulsifier with an HLB value 15, and water to obtain water phase B, and step 2 Add the obtained emulsion a into the water phase B under stirring and continue to stir for emulsification to obtain emulsion b for later use, then mix potassium hydroxide with water to obtain a potassium hydroxide solution; then add the emulsion b obtained in step 3 under stirring Carry out saponification reaction in potassium hydroxide solution to obtain soap-based lubricants, and then carry out inspection and testing on each batch of products to check whether the specific gravity, pH value and other indicators of the products meet the quality requirements, and do a sample test for each batch, and it is qualified The finished product is directly discharged through gravity flow, and finally the qualified product enters the automatic packaging machine through the feeding pump from the outlet of the open...
Embodiment 2
[0030] In embodiment one, add following operation:
[0031] When mixing stearic acid and emulsifier in step 1, the rotating speed of the stirrer is kept at 1000~1200rpm, and the stirring is carried out for 20-30min.
[0032] First heat the base oil, when the oil temperature reaches 80-100°C, add stearic acid and an emulsifier with an HLB value 15, and water to obtain water phase B, and step 2 Add the obtained emulsion a into the water phase B under stirring and continue to stir for emulsification to obtain emulsion b for later use, then mix potassium hydroxide with water to obtain a potassium hydroxide solution; then add the emulsion b obtained in step 3 under stirring Carry out saponification reaction in potassium hydroxide solution to obtain soap-based lubricants, and then carry out inspection and testing on each batch of products to check whether the specific gravity, pH value and other indicators of the products meet the quality requirements, and do a sample test for each...
PUM
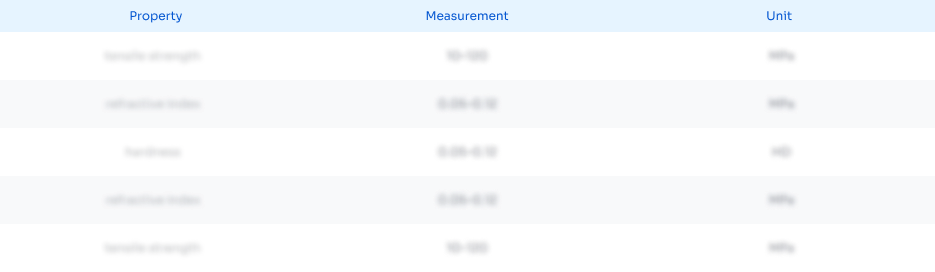
Abstract
Description
Claims
Application Information

- R&D Engineer
- R&D Manager
- IP Professional
- Industry Leading Data Capabilities
- Powerful AI technology
- Patent DNA Extraction
Browse by: Latest US Patents, China's latest patents, Technical Efficacy Thesaurus, Application Domain, Technology Topic, Popular Technical Reports.
© 2024 PatSnap. All rights reserved.Legal|Privacy policy|Modern Slavery Act Transparency Statement|Sitemap|About US| Contact US: help@patsnap.com