Novel composite water-based rust conversion primer and preparation method thereof
A rust conversion, water-based technology, applied in primers, coatings, anti-corrosion coatings, etc., can solve the problems of complex implementation process, corrosion of steel substrate, low efficiency, etc.
- Summary
- Abstract
- Description
- Claims
- Application Information
AI Technical Summary
Problems solved by technology
Method used
Image
Examples
Embodiment 1
[0026] Add 10.0g of deionized water into the three-necked flask, then add 1.0g of emulsion stabilizer EE, heat in a water bath to 70°C, wait until the emulsion stabilizer EE is fully dissolved in water, cool down to room temperature, and take 10.0g for later use. Add 60.0 g of styrene, acrylic acid copolymer emulsion and 30.0 g of water-based acrylic emulsion into beaker A, add 5.0 g of the reagent prepared above under the stirring condition of rotating speed of 600 r / min, stir for 5-10 min, and prepare water-based polymer emulsion for later use. In B beaker, dissolve 1.5g of dispersant (LD-6302) in 50.0g of deionized water, add 15.0g of modified aluminum tripolyphosphate, 20.0g of sericite, and 15.0g of kaolin under the condition of magnetic stirring or mechanical stirring until mixing Uniformly, the pigment slurry is obtained. Take the C beaker and add 46.0g of water-based polymer emulsion, add 30.0g of pigment slurry under stirring, stir evenly, then add 8g of prepared rust...
Embodiment 2
[0028] Add 10.0g of deionized water into the three-necked flask, then add 1.0g of emulsion stabilizer EE, heat in a water bath to 70°C, wait until the emulsion stabilizer EE is fully dissolved in water, cool down to room temperature, and take 10.0g for later use. Add 50.0 g of styrene, acrylic acid copolymer emulsion and 40.0 g of water-based acrylic emulsion into beaker A, add 5.0 g of the above-prepared reagent under the stirring condition of rotating speed of 600 r / min, stir for 5-10 minutes, and prepare water-based polymer emulsion for later use. In B beaker, dissolve 1.5g of dispersant (LD-6302) in 50.0g of deionized water, add 15.0g of modified aluminum tripolyphosphate, 20.0g of sericite, and 15.0g of kaolin under the condition of magnetic stirring or mechanical stirring until mixing Uniformly, the pigment slurry is obtained. Take the C beaker and add 52.0g of water-based polymer emulsion, add 25.0g of pigment filler under stirring, stir evenly, then add 8g of prepared ...
Embodiment 3
[0030] Add 10.0g of deionized water into the three-necked flask, then add 1.0g of emulsion stabilizer EE, heat in a water bath to 70°C, wait until the emulsion stabilizer EE is fully dissolved in water, cool down to room temperature, and take 10.0g for later use. Add 40.0 g of styrene, acrylic acid copolymer emulsion and 50.0 g of water-based acrylic emulsion into beaker A, add 5.0 g of the above-prepared reagent under the stirring condition of rotating speed of 600 r / min, stir for 5-10 min, and prepare water-based polymer emulsion for later use. In B beaker, dissolve 1.5g of dispersant (LD-6302) in 50.0g of deionized water, add 15.0g of modified aluminum tripolyphosphate, 20.0g of sericite, and 15.0g of kaolin under the condition of magnetic stirring or mechanical stirring until mixing Uniformly, the pigment slurry is obtained. Take the C beaker and add 58.0g of water-based polymer emulsion, add 25.0g of pigment slurry under stirring, stir evenly, then add 8g of prepared rust...
PUM
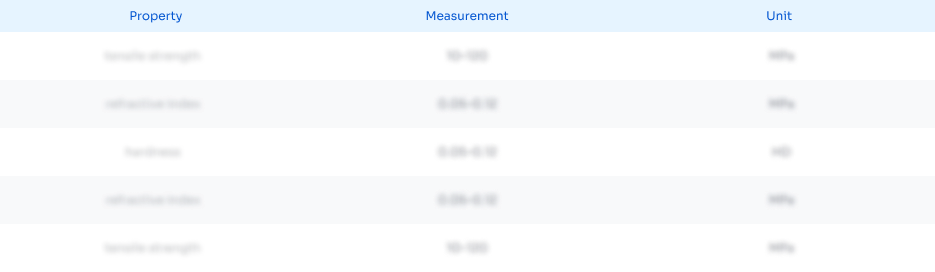
Abstract
Description
Claims
Application Information

- R&D
- Intellectual Property
- Life Sciences
- Materials
- Tech Scout
- Unparalleled Data Quality
- Higher Quality Content
- 60% Fewer Hallucinations
Browse by: Latest US Patents, China's latest patents, Technical Efficacy Thesaurus, Application Domain, Technology Topic, Popular Technical Reports.
© 2025 PatSnap. All rights reserved.Legal|Privacy policy|Modern Slavery Act Transparency Statement|Sitemap|About US| Contact US: help@patsnap.com