Sealing strip for steel doors and windows
A technology for sealing strips and doors and windows, which is applied in the field of material preparation, can solve the problems of affecting heat insulation performance, poor sealing performance, reduced dust resistance and water resistance, etc., and achieves low price, good thermal stability, and flame retardant performance. good effect
- Summary
- Abstract
- Description
- Claims
- Application Information
AI Technical Summary
Problems solved by technology
Method used
Image
Examples
Embodiment 1
[0026] Concrete raw material is weighed by table 1, and step preparation step is as follows:
[0027] (1) Add chlorinated polyethylene, butyl rubber, carbon black, calcium carbonate, plasticizer, silicon nitride whiskers, basic magnesium sulfate whiskers, and potassium titanate whiskers into a high-speed mixer, and heat up to 90 ℃, mix for 30min;
[0028] (2) Add the remaining raw materials to the mixture in step (1), continue mixing for 30 minutes, and leave to age for 5 hours;
[0029] (3) The extrusion temperature of the twin-screw extruder is set to be 190° C., and the screw speed is 200 rpm, and the product obtained in step (2) is added to the twin-screw extruder, and granulated through melt blending extrusion, The above-mentioned mixed materials were pressed into the desired shape of the sealing strip by using a hot press at 130°C.
Embodiment 2
[0031] (1) Add chlorinated polyethylene, butyl rubber, carbon black, calcium carbonate, plasticizer, silicon nitride whiskers, basic magnesium sulfate whiskers, and potassium titanate whiskers into a high-speed mixer, and heat up to 100 ℃, mix for 20min;
[0032] (2) Add remaining raw materials to the mixture in step (1), continue mixing for 40 minutes, and leave to age for 6 hours;
[0033] (3) The extrusion temperature of the twin-screw extruder is set to be 220° C., and the screw speed is 250 rpm, and the product obtained in step (2) is added to the twin-screw extruder, and granulated through melt blending extrusion, The above-mentioned mixed materials were pressed into the desired shape of the sealing strip by using a hot press at 160°C.
Embodiment 3
[0035] (1) Add chlorinated polyethylene, butyl rubber, carbon black, calcium carbonate, plasticizer, silicon nitride whiskers, basic magnesium sulfate whiskers, and potassium titanate whiskers into a high-speed mixer, and heat up to 100 ℃, mix for 30min;
[0036] (2) Add the remaining raw materials to the mixture in step (1), continue mixing for 40 minutes, and leave to age for 5 hours;
[0037] (3) The extrusion temperature of the twin-screw extruder is set to be 200° C., and the screw speed is 250 rpm, and the product obtained in step (2) is added to the twin-screw extruder, and granulated through melt blending extrusion, The above-mentioned mixed materials were pressed into the desired shape of the sealing strip by using a hot press at 160°C.
PUM
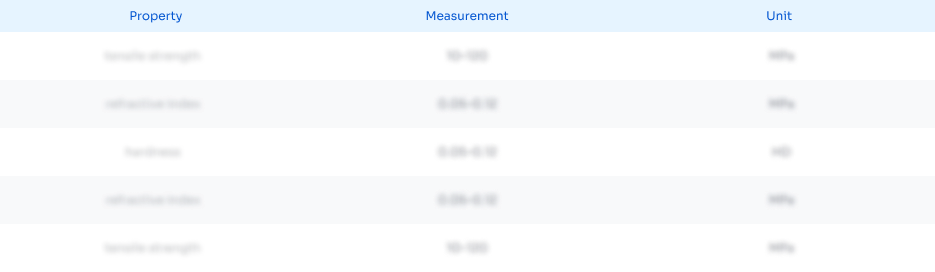
Abstract
Description
Claims
Application Information

- R&D
- Intellectual Property
- Life Sciences
- Materials
- Tech Scout
- Unparalleled Data Quality
- Higher Quality Content
- 60% Fewer Hallucinations
Browse by: Latest US Patents, China's latest patents, Technical Efficacy Thesaurus, Application Domain, Technology Topic, Popular Technical Reports.
© 2025 PatSnap. All rights reserved.Legal|Privacy policy|Modern Slavery Act Transparency Statement|Sitemap|About US| Contact US: help@patsnap.com