Water-dispersion-resistant synchronous grouting material for water-rich stratum
A water-resistant dispersion and synchronous grouting technology, applied in the field of grouting materials, can solve the problems of easy to be washed by water, dilution, poor water-resistant dispersion performance, affecting project quality, etc., to improve the injectability and water-resistant dispersion performance. Good, high coagulation effect
- Summary
- Abstract
- Description
- Claims
- Application Information
AI Technical Summary
Problems solved by technology
Method used
Image
Examples
Embodiment 1
[0030] In this embodiment, 2000g of water-resistant and dispersed synchronous grouting material suitable for water-rich formations is made of the following quality raw materials: 664g of 42.5-grade ordinary Portland cement that meets the requirements of the "General Portland Cement" standard, and meets the requirements of the "Construction Portland Cement" standard. "Sand" standard requirements, fineness modulus 2.5 ~ 3.0, mud content <1.0% river sand 1327g, nano-silicon modified magnesium lithium silicate 7g, sodium polyacrylate 0.27g, guar gum ether 1g, high performance reducer Aqua 0.73g;
[0031] After mixing the raw materials of 2000 g of the above materials, put them into a mortar mixer and stir for 120 seconds to make the raw materials evenly mixed. Then add the water of 1600g and stir for 120 seconds again, make finished material L 1 .
Embodiment 2
[0033] In this embodiment, 2000g of water-resistant and dispersed synchronous grouting material suitable for water-rich formations is made of the following quality raw materials: 664g of 42.5-grade ordinary Portland cement that meets the requirements of the "General Portland Cement" standard, and meets the requirements of the "Construction Portland Cement" standard. "Sand" standard requirements, fineness modulus 2.5 ~ 3.0, mud content <1.0% river sand 1327g, nano-silicon modified magnesium lithium silicate 6.67g, sodium polyacrylate 0.53g, guar gum ether 1g, high performance Water reducer 0.8g;
[0034] After mixing the above-mentioned 2000 g of each raw material in total, put it into a mortar mixer and stir for 120 seconds, so that each raw material is uniformly mixed. Then add the water of 1600g and stir for 120 seconds again, make finished material L 2 .
Embodiment 3
[0036]In this embodiment, 2000g of water-resistant and dispersed synchronous grouting material suitable for water-rich formations is made of the following quality raw materials: 994g of 42.5-grade ordinary Portland cement required by the "Universal Portland Cement" standard, which meets the requirements of "Construction Use Sand" standard requirements, fineness modulus 2.5 ~ 3.0, mud content < 1.0% river sand 993g, nano-silicon modified magnesium lithium silicate 9.6g, sodium polyacrylate 0.4g, guar gum ether 2g, high performance reducer Aqua 1g;
[0037] After mixing the above-mentioned 2000 g of each raw material in total, put it into a mortar mixer and stir for 120 seconds, so that each raw material is uniformly mixed. Then add the water of 1500g and stir for 120 seconds again, make finished material L 3 .
PUM
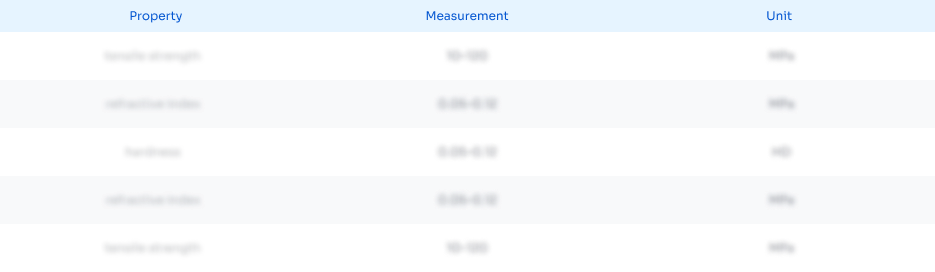
Abstract
Description
Claims
Application Information

- R&D
- Intellectual Property
- Life Sciences
- Materials
- Tech Scout
- Unparalleled Data Quality
- Higher Quality Content
- 60% Fewer Hallucinations
Browse by: Latest US Patents, China's latest patents, Technical Efficacy Thesaurus, Application Domain, Technology Topic, Popular Technical Reports.
© 2025 PatSnap. All rights reserved.Legal|Privacy policy|Modern Slavery Act Transparency Statement|Sitemap|About US| Contact US: help@patsnap.com