Surface-mounted fuse based on low-temperature co-fired ceramic technology and preparation method thereof
A technology of low-temperature co-fired ceramics and surface mounting, which is applied in the manufacture of fuses, emergency protection devices, emergency protection devices, etc. It can solve problems such as diffusion surfaces and unevenness, achieve good wettability, prevent penetration, and meet performance requirements Effect
- Summary
- Abstract
- Description
- Claims
- Application Information
AI Technical Summary
Problems solved by technology
Method used
Image
Examples
Embodiment 1
[0050] A method for preparing a surface-mount fuse based on low-temperature co-fired ceramic technology in Example 1 includes the following steps:
[0051] Step 1, preparing low temperature co-fired ceramic powder
[0052] Weigh 30 parts of calcium oxide powder, 25 parts of boron oxide powder, and 35 parts of silicon oxide powder, put them into a 500ml ball mill jar made of zirconia, and perform ball milling. The ball-to-material ratio is 4:1, and the dry powder ball mills for 4 hours , after cooling, ultrasonically pass through an 80-mesh sieve to separate and obtain mixed powder;
[0053] Take a 250ml platinum crucible and preheat it in a high-temperature furnace at 1250°C for 30 minutes, then place the mixed powder in the platinum crucible, and heat the mixed powder in a high-temperature furnace at 1250°C for 30 minutes. When it is completely melted, take out the platinum crucible to obtain the molten material, and place the molten material in deionized water for water que...
Embodiment 2
[0086] The preparation method of the surface mount fuse of this embodiment 2 is the same as that of embodiment 1, and its difference from embodiment 1 is:
[0087] The mixed powder in step 1 of Example 2 includes 35 parts of calcium oxide powder, 30 parts of boron oxide powder, and 40 parts of silicon oxide powder; in step 1, when preparing low-temperature co-fired ceramic powder, two low-temperature co-fired The ceramic powders are respectively, one is: it contains 85 parts of Ca-B-Si series glass-ceramic powder and 13 parts of zirconia powder, which is used for the heat insulation layer; the other is: it contains Ca-B-Si series 85 parts of glass-ceramic powder and 16 parts of zirconia powder are used for the arc-extinguishing layer; the solid content in the low-temperature co-fired ceramic slurry for the heat-insulation layer is 76%, and the arc-extinguishing layer uses the low-temperature co-fired ceramic slurry The solids content was 68%.
[0088] The fuse electrode paste...
Embodiment 3
[0092] The preparation method of the surface mount fuse of this embodiment 3 is the same as that of embodiment 1, and its difference from embodiment 1 is:
[0093] The mixed powder in step 1 of Example 3 includes 40 parts of calcium oxide powder, 35 parts of boron oxide powder, and 45 parts of silicon oxide powder; in step 1, when preparing low-temperature co-fired ceramic powder, two kinds of low-temperature co-fired The ceramic powders are respectively, one is: it contains 90 parts of Ca-B-Si series glass-ceramic powder and 15 parts of zirconia powder, which is used for the heat insulation layer; the other is: it contains Ca-B-Si series 90 parts of glass-ceramic powder and 20 parts of zirconia powder are used for the arc-extinguishing layer; the solid content in the low-temperature co-fired ceramic slurry for the heat-insulating layer is 80%, and the arc-extinguishing layer uses 80% of the solid content in the low-temperature co-fired ceramic slurry The solid content is 70%....
PUM
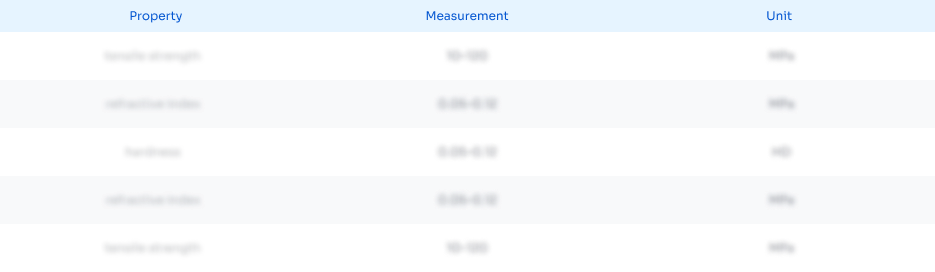
Abstract
Description
Claims
Application Information

- Generate Ideas
- Intellectual Property
- Life Sciences
- Materials
- Tech Scout
- Unparalleled Data Quality
- Higher Quality Content
- 60% Fewer Hallucinations
Browse by: Latest US Patents, China's latest patents, Technical Efficacy Thesaurus, Application Domain, Technology Topic, Popular Technical Reports.
© 2025 PatSnap. All rights reserved.Legal|Privacy policy|Modern Slavery Act Transparency Statement|Sitemap|About US| Contact US: help@patsnap.com