Preparation method of high-strength building plastic formwork with strong nail-holding power
A plastic formwork and nail-holding force technology, which is applied to the preparation of building components on site, construction, building construction, etc., can solve the problems of not being able to improve the nail-holding force, increase costs, and waste man-hours
- Summary
- Abstract
- Description
- Claims
- Application Information
AI Technical Summary
Problems solved by technology
Method used
Image
Examples
Embodiment 1
[0020] The first step, preparation of flame retardant enhanced microcapsules: in parts by weight, 38 parts of halogen-free flame retardant 2,3-dimethyl-2,3-diphenylbutane, 18 parts of melamine phosphate, 71 parts 2 parts of natural rubber emulsion wall material, 2 parts of emulsifier sodium cyclamate, 23 parts of chloroether resin emulsion, and then use a high-speed dispersing homogenizer to mix at 8000~10000r / min for 9 minutes, and then homogenize Homogenize for 9 minutes at a pressure of 28MPa until the emulsion does not separate. After cooling to room temperature, immediately place it in a spray dryer and spray dry. The temperature is 90°C and then the microcapsule powder is collected to obtain the flame-retardant reinforced microcapsules; the second step, in parts by weight, weighs 69 parts of phenolic epoxy vinyl ester resin, 30 parts of reinforcing filler diacid green Rock powder, 15 parts of flame-retardant reinforced microcapsules and 58 parts of trans-1,4-polyisoprene...
Embodiment 2
[0024] The first step, preparation of flame retardant enhanced microcapsules: by weight, 35 parts of halogen-free flame retardant dicumyl oligomer, 15 parts of melamine phosphate, 67 parts of natural rubber emulsion wall material, emulsifier Mix 1 part of sodium alizarin sulfonate and 17 parts of chloroether resin emulsion evenly, then use a high-speed dispersing homogenizer to mix at 8000r / min for 6 minutes, and then homogenize at a homogenizing pressure of 22MPa for 6 minutes until the emulsion does not separate. After cooling to room temperature, place it in a spray dryer immediately, and spray dry it. The feed flow rate is 200mL / h, the spray pressure is 0.3MPa, the inlet air temperature is 160°C, and the outlet temperature is 90°C, and then the microcapsule powder is collected to obtain The flame-retardant reinforced microcapsules;
[0025] The second step, in parts by weight, weighs 63 parts of tetrabromobisphenol A type epoxy vinyl ester resins, 12 parts of flame-retarda...
PUM
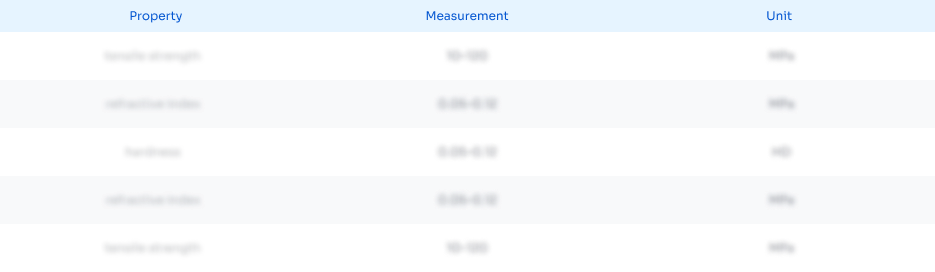
Abstract
Description
Claims
Application Information

- R&D
- Intellectual Property
- Life Sciences
- Materials
- Tech Scout
- Unparalleled Data Quality
- Higher Quality Content
- 60% Fewer Hallucinations
Browse by: Latest US Patents, China's latest patents, Technical Efficacy Thesaurus, Application Domain, Technology Topic, Popular Technical Reports.
© 2025 PatSnap. All rights reserved.Legal|Privacy policy|Modern Slavery Act Transparency Statement|Sitemap|About US| Contact US: help@patsnap.com