A kind of synthetic method of 2,3,5-trichloropyridine
A triclopyridine and synthesis method technology, applied in the field of pesticide chemical industry, can solve the problems of fewer synthesis steps, harsh conditions, and environmental pollution, and achieve the effects of less heavy metal pollution, mild reaction conditions, and simple post-treatment
- Summary
- Abstract
- Description
- Claims
- Application Information
AI Technical Summary
Problems solved by technology
Method used
Image
Examples
Embodiment 1
[0033] Add chloral (240 grams, 1.62 moles) and acrylonitrile (95 grams, 1.79 moles) to the flask and mix well, then add 12 grams of cuprous chloride, 0.24 grams of hydroquinone and 2.4 grams of polyethylene glycol Alcohol 200, reacted at 85°C for 30 hours, then filtered, separated the catalyst, and then distilled under reduced pressure. When no liquid flowed out, 2,4,4-trichloro-4-formylbutyronitrile reaction liquid was obtained. (Wherein, the quality of 2,4,4-trichloro-4-formylbutyronitrile is 310 grams, 1.54 moles, purity 95.5%, yield 94.9%), need not separate, then be warming up to 80 ℃, slowly pass through Add 120 grams (3.28 moles) of hydrogen chloride gas and react for 3 hours. After the reaction is complete, distill under reduced pressure to obtain 240 grams (3.28 moles) of 2,3,5-trichloropyridine with a purity of 99.2% and a yield of 80.8%.
Embodiment 2
[0035] Add chloral (240 grams, 1.62 moles) and acrylonitrile (95 grams, 1.79 moles) in the flask and mix well, then add 12 grams of cuprous chloride, 0.24 grams of hydroquinone and 2.4 gram of polyethylene glycol 200, reacted at 85°C for 30 hours, then filtered, separated the catalyst, and then distilled under reduced pressure. When no liquid flowed out, 2,4,4-trichloro-4-formylbutyl Nitrile reaction liquid, (wherein, the quality of 2,4,4-trichloro-4-formylbutyronitrile is 309 grams, 1.54 moles, purity 95.9%, yield 94.6%), need not separate, then be heated up to 80 ℃, 120 g (3.28 moles) of hydrogen chloride gas was slowly introduced into it, and reacted for 3 hours. After the reaction was complete, it was distilled under reduced pressure to obtain 238 g of 2,3,5-trichloropyridine with a purity of 99.0% and a yield of 80.1%.
Embodiment 3
[0037] Add chloral (240 grams, 1.62 moles) and acrylonitrile (172 grams, 3.24 moles) to the flask and mix well, then add 12 grams of cuprous chloride, 0.24 grams of hydroquinone and 2.4 grams of polyethylene glycol Alcohol 200, reacted at 85°C for 30 hours, then filtered, separated the catalyst, and then distilled under reduced pressure. When no liquid flowed out, 2,4,4-trichloro-4-formylbutyronitrile reaction liquid was obtained. (Wherein, the quality of 2,4,4-trichloro-4-formylbutyronitrile is 311 grams, 1.54 moles, purity 96.5%, yield 95.3%), need not separate, then be warming up to 80 ℃, slowly pass through Add 120 g (3.28 moles) of hydrogen chloride gas and react for 3 hours. After the reaction is complete, distill under reduced pressure to obtain 241.7 g of 2,3,5-trichloropyridine with a purity of 99.5% and a yield of 81.4%.
PUM
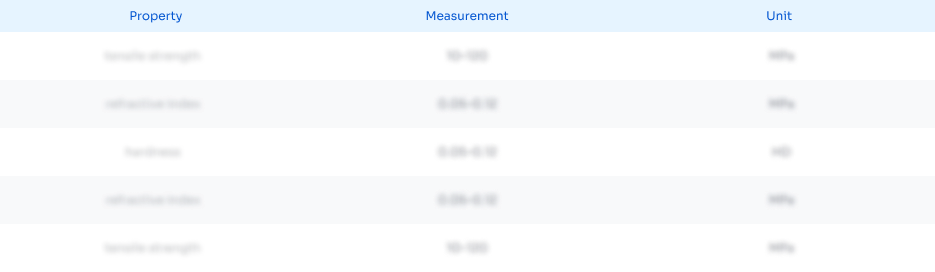
Abstract
Description
Claims
Application Information

- Generate Ideas
- Intellectual Property
- Life Sciences
- Materials
- Tech Scout
- Unparalleled Data Quality
- Higher Quality Content
- 60% Fewer Hallucinations
Browse by: Latest US Patents, China's latest patents, Technical Efficacy Thesaurus, Application Domain, Technology Topic, Popular Technical Reports.
© 2025 PatSnap. All rights reserved.Legal|Privacy policy|Modern Slavery Act Transparency Statement|Sitemap|About US| Contact US: help@patsnap.com