Light inorganic honeycomb core composite fireproof plate and preparation method thereof
A technology of honeycomb core and fireproof board, which is applied in the direction of manufacturing tools, ceramic products, ceramic molding machines, etc., and can solve the problems that fireproof boards cannot meet the needs of high fire-resistant materials, property loss and other losses, and limit the scope of market applications. To achieve the effect of expanding the scope of market application, low comprehensive cost, and broadening the field of use
- Summary
- Abstract
- Description
- Claims
- Application Information
AI Technical Summary
Problems solved by technology
Method used
Image
Examples
Embodiment 1
[0035] A lightweight inorganic honeycomb core composite fireproof board:
[0036] 1) Preparation of composite foaming agent mother liquor: start the heating belt stirring reactor, put in 52% deionized water, 35% sodium lauryl sulfate, and 10% tea saponin, heat to 85°C and fully react for 2 hours, then cool down to At 40°C, put 1% Cathone into the reactor, stir at constant temperature for 30 minutes, discharge, and set aside;
[0037] 2) Preparation of inorganic main body slurry: start the adjustable speed horizontal mixing mixer, put 21.5% tap water, 75% gypsum powder, 1% potassium sulfate, 0.5% polycarboxylate water reducer, 2% polypropylene fiber into the mixer, Stir and disperse at a speed of 400r / min for 3 minutes;
[0038] 3) Preparation of thin slurry for honeycomb core composite board: Dilute the prepared composite foaming agent mother liquor with water at 1:30, use physical foaming method to produce light foam through air compression foaming agent, and use the corresp...
Embodiment 2
[0041] A lightweight inorganic honeycomb core composite fireproof board:
[0042] 1) Preparation of composite blowing agent mother liquor: start the heating belt stirring reactor, put in 61% deionized water, 30% α-olefin sulfonate, 6% fatty alcohol, heat to 85°C for full reaction for 1 hour, then cool down to 40°C ℃, put 2% sodium benzoate into the reaction kettle, stir at constant temperature for 30min, discharge and set aside;
[0043] 2) Preparation of inorganic main slurry: start the adjustable speed horizontal mixing mixer, mix 25.7% tap water, 50% lightly burned magnesium oxide powder, 14% anhydrous magnesium sulfate, 0.3% melamine superplasticizer, 10% wood flour fiber Put it into the mixer, stir and disperse at a speed of 400r / min for 3 minutes;
[0044] 3) Preparation of thin slurry for honeycomb core composite board: Dilute the prepared composite foaming agent mother liquor with water at 1:40, use physical foaming method to produce light foam through air compression...
Embodiment 3
[0047] A lightweight inorganic honeycomb core composite fireproof board:
[0048] 1) Preparation of composite foaming agent mother liquor: start the heating belt stirring reactor, put in 61% deionized water, 30% fatty acid polyoxyethylene ester, 6% polyvinyl alcohol, heat to 85 ° C for 1 hour, and then cool down to 40 °C ℃, put 2% organic sulfur into the reaction kettle, stir at constant temperature for 30min, discharge and set aside;
[0049] 2) Preparation of inorganic main body slurry: Start the adjustable speed horizontal mixing mixer, put 33% tap water, 45% light-burned magnesium oxide powder, 12% magnesium silicate, 0.3% naphthalene-based water reducer, and 10% basalt fiber into the mixer In the process, stir and disperse for 3 minutes at a speed of 400r / min;
[0050] 3) Preparation of thin slurry for honeycomb core composite board: Dilute the prepared composite foaming agent mother liquor with water at 1:40, use physical foaming method to produce light foam through air...
PUM
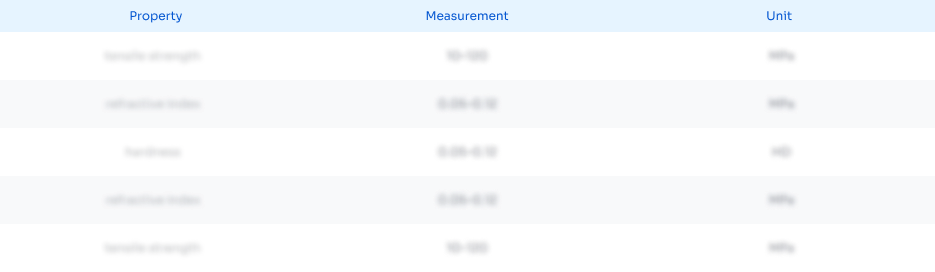
Abstract
Description
Claims
Application Information

- R&D
- Intellectual Property
- Life Sciences
- Materials
- Tech Scout
- Unparalleled Data Quality
- Higher Quality Content
- 60% Fewer Hallucinations
Browse by: Latest US Patents, China's latest patents, Technical Efficacy Thesaurus, Application Domain, Technology Topic, Popular Technical Reports.
© 2025 PatSnap. All rights reserved.Legal|Privacy policy|Modern Slavery Act Transparency Statement|Sitemap|About US| Contact US: help@patsnap.com