Diesel machine waste gas purification process
A purification process and exhaust gas purification technology, applied in the direction of machines/engines, gas treatment, mechanical equipment, etc., can solve the problems of incomplete combustion of fuel mixture, unfavorable small enterprises to put into use, high operating costs, etc., to achieve ingenious structural design, The effect of low input cost and easy popularization
- Summary
- Abstract
- Description
- Claims
- Application Information
AI Technical Summary
Problems solved by technology
Method used
Image
Examples
Embodiment 1
[0082] The invention provides a multi-stage purification equipment for purifying exhaust gas released by diesel engines, comprising the following steps:
[0083] 1. Waste gas combustion purification stage:
[0084] S1, first start the electric cylinder 150 of the exhaust gas purification equipment of the diesel engine to drive the charcoal rack 140 to rise until the charcoal plate 142 is exposed, and then put some charcoal on the charcoal plate 142 at equal intervals;
[0085] S2. Restart the electric cylinder 150 to reset the piston rod, and the charcoal rack 140 falls into the combustion box 120 under the force of its own weight;
[0086] S3, then connect the power supply of the electric heating tube 180 to make it work to generate heat, enter the combustion box 120 through the heat transfer port 122, and then bake the charcoal to turn red;
[0087] S4, turn off the power supply of the electric heating tube 180, then start the forward and reverse motor 170 to make it work i...
PUM
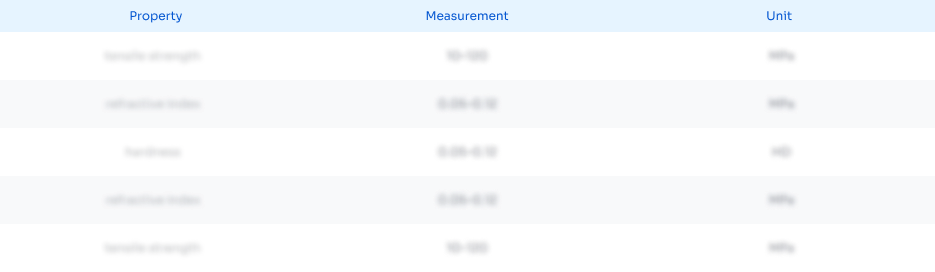
Abstract
Description
Claims
Application Information

- R&D
- Intellectual Property
- Life Sciences
- Materials
- Tech Scout
- Unparalleled Data Quality
- Higher Quality Content
- 60% Fewer Hallucinations
Browse by: Latest US Patents, China's latest patents, Technical Efficacy Thesaurus, Application Domain, Technology Topic, Popular Technical Reports.
© 2025 PatSnap. All rights reserved.Legal|Privacy policy|Modern Slavery Act Transparency Statement|Sitemap|About US| Contact US: help@patsnap.com