Printing and dyeing device for chemical fabric processing and using method thereof
A technology of chemical fiber cloth and dye, which is applied in the field of chemical fiber cloth processing, can solve the problems of affecting output and quality, breaking the fabric, stretching, etc., and achieve the effect of improving efficiency and quality, avoiding extrusion or stretching, and strengthening quality
- Summary
- Abstract
- Description
- Claims
- Application Information
AI Technical Summary
Problems solved by technology
Method used
Image
Examples
Embodiment 1
[0038] Such as Figure 1-Figure 6As shown, the printing and dyeing device for chemical fiber cloth processing includes a dye box 1, a raw material roll 3, and a receiving roll 7. A first bracket 2 is arranged on one side of the dye box 1 to support the raw material roll 3, and the first bracket 2 is connected to the raw material roll. 3. To wind the chemical fiber cloth raw material, the other side of the dye box 1 is provided with a second support 8, and the second support 8 is connected with a take-up roller 7 for winding the printed and dyed chemical fiber cloth, the raw material roller 3 and the take-up roller 7 The rear end is equipped with a third sprocket 30, and a heating pipe 19 is arranged at the inner bottom of the dye box 1 to heat the dye 18. The dye 18 is arranged in the dye box 1, and a liquid level detector 17 is arranged on the inner wall of the dye box 1. To detect the liquid level, there is a feed inlet 29 on the dye box 1 close to the raw material roller 3,...
Embodiment 2
[0040] The difference between this embodiment and embodiment 1 is:
[0041] The first feed roller 12, the second feed roller 16 are rotationally connected with the dye box 1, the first feed roller 12, the second feed roller 16 are provided with two places in the dye box 1, the first feed roller 12, When the second feeding roller 16 rotates, the chemical fiber cloth is moved forward to ensure that the chemical fiber cloth has a moving force before and after printing and dyeing.
[0042] The present invention also provides a method for using a printing and dyeing device for processing chemical fiber cloth, which is applied to the above printing and dyeing device for processing chemical fiber cloth. The specific method of use is as follows:
[0043] a, pass the chemical fiber cloth on the raw material roll 3 between the first feed roll 12 and the second feed roll 16, the dye 18 enters the dye tank 1 through the feed pipe 27, and the liquid level detector 17 checks the liquid leve...
PUM
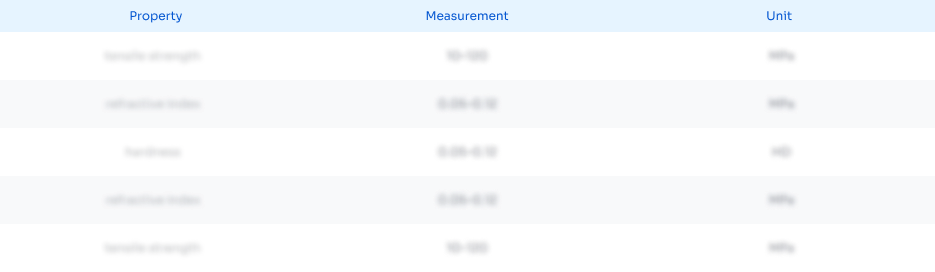
Abstract
Description
Claims
Application Information

- R&D
- Intellectual Property
- Life Sciences
- Materials
- Tech Scout
- Unparalleled Data Quality
- Higher Quality Content
- 60% Fewer Hallucinations
Browse by: Latest US Patents, China's latest patents, Technical Efficacy Thesaurus, Application Domain, Technology Topic, Popular Technical Reports.
© 2025 PatSnap. All rights reserved.Legal|Privacy policy|Modern Slavery Act Transparency Statement|Sitemap|About US| Contact US: help@patsnap.com