Continuous flow microreactor, manufacturing method and application
A micro-reactor and catalytic reaction technology, which is applied in chemical instruments and methods, chemical/physical/physical-chemical reactors, carboxylic acid nitrile preparation, etc., can solve problems such as poor temperature uniformity, many by-products, and slow heating rate
- Summary
- Abstract
- Description
- Claims
- Application Information
AI Technical Summary
Problems solved by technology
Method used
Image
Examples
Embodiment 1
[0053] Example 1: Preparation of 3D printed microreactor unit
[0054] According to the set formula (vol.%): nickel zinc ferrite (46.0%), polyacrylate (2.3%), polyvinyl alcohol (2.0%), polyethylene glycol and glycerin are both (3.5%) , the rest is deionized water, add polyacrylate, polyethylene glycol, polyvinyl alcohol and glycerin to deionized water, stir well and get a premixed solution, add nickel zinc ferrite powder to the beaker and stir, After all the powder is added, put it on the mixer and stir for 8 hours, then add hydrochloric acid to adjust the pH value of the mud to 7, and put it in a tank for standby; the air pump pressure of the printing equipment is 5bar, the diameter of the extrusion needle is 0.6mm, and the printing speed is 20 mm s -1 , When the slice layer thickness is 0.54mm, the printed samples of nano-ferrite microreactors with different apertures can be obtained, and after 24 h drying, 900 o C above sintering to obtain the microreactor unit.
[0055]...
Embodiment 2
[0056] Embodiment 2: ZIF-8 grows in microreactor unit channel
[0057] APTES was used to assist the growth of ZIF-8 in the microreactor unit channel. After adding 0.05mmol APTES to 20ml of toluene solution, put 2g of washed and dried microreactor unit into it, 110 o C was refluxed for 24h, the cooled sample was thoroughly washed with methanol, and o C vacuum dried for 24 h for later use; Zn(NO 3 ) 2 ·6H 2 O (3mmol) and 2-methylimidazole (12mmol) were dissolved in 30ml and 20ml of anhydrous methanol respectively, until the solid was completely dissolved, the modified microreactor unit was put into the methanol solution of imidazole, and the Zn salt solution Quickly add in the imidazole solution under stirring, transfer the mixture to a 100mL polytetrafluoro reactor after stirring for 5min, seal it, and o C for 24 h. After cooling to room temperature, the mother liquor was removed from the mixture, and the microreactor was soaked and washed 4 times with anhydrous methanol....
Embodiment 3
[0058] Embodiment 3: the making and usage of microreactor unit
[0059] In the first step, the catalytic reaction unit obtained in Example 2 is superimposed on the lower end of the quartz tube as a catalytic reaction zone, and a microreactor unit with a certain height unloaded catalyst is superimposed on it as a preheating section, and a temperature sensor is implanted in the two-section contact surface. Lay glass beads with an outer diameter of 2.5mm on the quartz tube, and connect a double-hole rubber stopper at the end, one of which is connected to nitrogen, and the other is connected to a Y-shaped mixer through a hose, and the two inlets of the mixer are connected to the constant flow pump , the storage tank, and the hose are connected, and the outlet port of the quartz tube is connected to the product collection pool for the collection of reaction products;
[0060] In the second step, the quartz tube assembled with the microchannel reactor unit is placed in the magnetic ...
PUM
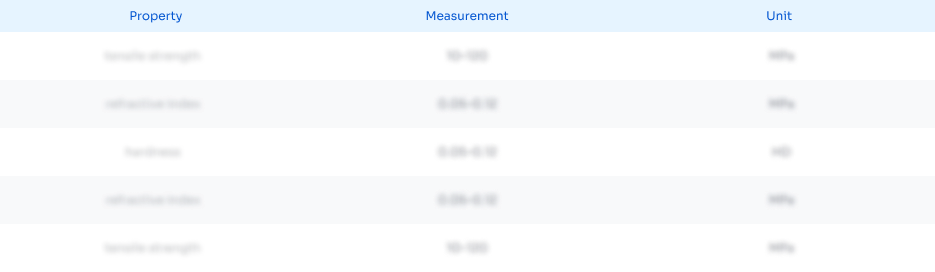
Abstract
Description
Claims
Application Information

- R&D Engineer
- R&D Manager
- IP Professional
- Industry Leading Data Capabilities
- Powerful AI technology
- Patent DNA Extraction
Browse by: Latest US Patents, China's latest patents, Technical Efficacy Thesaurus, Application Domain, Technology Topic, Popular Technical Reports.
© 2024 PatSnap. All rights reserved.Legal|Privacy policy|Modern Slavery Act Transparency Statement|Sitemap|About US| Contact US: help@patsnap.com