All-solid-state chip large-angle optical beam forming system
A beamforming and chip-based technology, applied in the field of all-solid-state chip-based large-angle optical beamforming systems, can solve the problems of limited wavelength range of laser tuning, affecting the application performance of OPA technology, and limited beam scanning angle, etc., to achieve small hardware complexity The effect of sacrificing degree, improving integrability, and simplifying hardware complexity
- Summary
- Abstract
- Description
- Claims
- Application Information
AI Technical Summary
Problems solved by technology
Method used
Image
Examples
Embodiment Construction
[0048] like figure 1 As shown, it is a schematic structural diagram of an all-solid-state chip-based large-angle optical beamforming system of the present invention, including:
[0049] A tunable laser source that will be above the source threshold I th The pumping current of the laser is injected into the gain region of the laser, and the single-mode laser with a wavelength of λ is independently emitted by the light source, and is transmitted from the front end of the laser to the semiconductor optical amplifier through the on-chip waveguide; the laser needs to be single-mode, that is, single longitudinal mode + single transverse mode The reasonable design of the waveguide cross section can easily ensure the single transverse mode; the control of the single longitudinal mode of the device is often more complicated.
[0050] Semiconductor optical amplifier, by injecting appropriate driving current, amplifies the laser power from the tunable laser source to a high enough level...
PUM
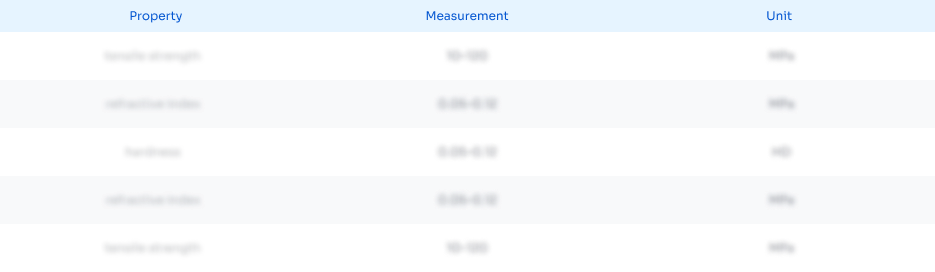
Abstract
Description
Claims
Application Information

- R&D
- Intellectual Property
- Life Sciences
- Materials
- Tech Scout
- Unparalleled Data Quality
- Higher Quality Content
- 60% Fewer Hallucinations
Browse by: Latest US Patents, China's latest patents, Technical Efficacy Thesaurus, Application Domain, Technology Topic, Popular Technical Reports.
© 2025 PatSnap. All rights reserved.Legal|Privacy policy|Modern Slavery Act Transparency Statement|Sitemap|About US| Contact US: help@patsnap.com