Waterless grinding mirror polishing process
A mirror polishing and water grinding technology, which is applied in the field of mirror processing, can solve the problems of uniform and inconsistent production quality, substandard sewage discharge, low production capacity, etc., and achieve the effect of solving uniform and inconsistent production quality, low processing cost and high production efficiency
- Summary
- Abstract
- Description
- Claims
- Application Information
AI Technical Summary
Problems solved by technology
Method used
Examples
Embodiment 1
[0019] An anhydrous grinding mirror polishing process, its preparation process comprises the following steps:
[0020] A. According to the size of the customer's product dimensions, the drag-type automatic polishing machine that meets the polishing running distance of the product is customized;
[0021] B. Choose from 24 to 960 polishing rods according to the customer's production capacity, and the distance between the polishing rods is from 60mm to 400mm, and then customize the appropriate process according to the quality standard of the mirror polishing of the customer's product surface (coarse polishing, medium polishing, fine polishing) throw);
[0022] C. The process of rough polishing, medium polishing and fine polishing needs to select the appropriate polishing carrier according to the removal amount of the customer's product surface.
Embodiment 2
[0024] In embodiment one, add following operation again:
[0025] In step B, the walnut grains and corncobs for coarse throwing will be between 6.5mm and 3.2mm, for medium throwing will be between 5.0mm and 1.6mm, and for fine throwing will be between 1.6mm and 0.5mm.
[0026] An anhydrous grinding mirror polishing process, its preparation process comprises the following steps:
[0027] A. According to the size of the customer's product dimensions, the drag-type automatic polishing machine that meets the polishing running distance of the product is customized;
[0028] B. Choose from 24 to 960 polishing rods according to the customer's production capacity, and the distance between the polishing rods is from 60mm to 400mm, and then customize the appropriate process according to the quality standard of the mirror polishing of the customer's product surface (coarse polishing, medium polishing, fine polishing) throw);
[0029] C. The process of rough polishing, medium polishing ...
Embodiment 3
[0031] In embodiment two, add following operation again:
[0032] In step B, the aluminum oxide, cerium oxide, and silicon carbide for rough polishing will be between 180# and 320#, the middle polishing will be between 400# and 800#, and the fine polishing will be between 1000# and 150nm.
[0033] An anhydrous grinding mirror polishing process, its preparation process comprises the following steps:
[0034] A. According to the size of the customer's product dimensions, the drag-type automatic polishing machine that meets the polishing running distance of the product is customized;
[0035] B. Choose from 24 to 960 polishing rods according to the customer's production capacity, and the distance between the polishing rods is from 60mm to 400mm, and then customize the appropriate process according to the quality standard of the mirror polishing of the customer's product surface (coarse polishing, medium polishing, fine polishing) throw);
[0036] C. The process of rough polishi...
PUM
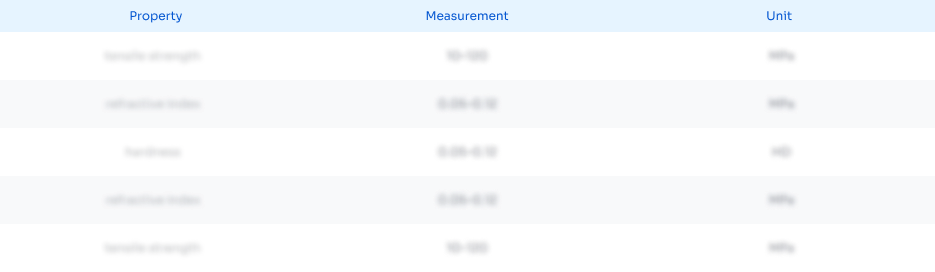
Abstract
Description
Claims
Application Information

- R&D
- Intellectual Property
- Life Sciences
- Materials
- Tech Scout
- Unparalleled Data Quality
- Higher Quality Content
- 60% Fewer Hallucinations
Browse by: Latest US Patents, China's latest patents, Technical Efficacy Thesaurus, Application Domain, Technology Topic, Popular Technical Reports.
© 2025 PatSnap. All rights reserved.Legal|Privacy policy|Modern Slavery Act Transparency Statement|Sitemap|About US| Contact US: help@patsnap.com