Nylon-based injection molding magnetic composite material and preparation method thereof
A magnetic composite material, nylon-based technology, applied in the magnetic direction of organic materials/organic magnetic materials, can solve the problems of low maximum magnetic energy product, low filling amount of magnetic inorganic fillers, etc., to ensure mechanical strength, increase filling amount, and magnetic energy positive effect
- Summary
- Abstract
- Description
- Claims
- Application Information
AI Technical Summary
Problems solved by technology
Method used
Image
Examples
preparation Embodiment 1
[0056] Preparation Example 1 (Preparation of dendritic silane-polyamide-amine coupling agent)
[0057] (1) Under the protection of nitrogen, combine 5.16kg of monomer A ethylenediamine tetracapronic acid and 8.16kg of monomer B3-(2-aminoethyl-(2-carboxyethyl)amino)propionic acid (monomer The molar ratio of A to monomer B is 1:4) Put it into an automatically controlled polymerization kettle with a stirrer, heat up to 90°C, and react for 3 hours until the reaction liquid becomes a clear and uniform liquid without bubbles, and the intermediate product E is obtained. ;
[0058] (2) Add 2.4 kg of monomer C ethylene diamine (molar ratio of monomer A to monomer A in step (1) 4:1) into the automatically controlled polymerizer with a stirrer containing the intermediate product E of step (1). ) And 8.84kg of monomer Dγ-aminopropyltriethoxysilane (the molar ratio of monomer A in step (1) is 4:1). When the temperature in the polymerization vessel is heated to 120°C, start stirring and continu...
Embodiment 1-8
[0060] The nylon-based injection molded magnetic composite material of the present invention was prepared according to the following method according to the charging ratio of each raw material in Table 1:
[0061] Step A: crush the nylon base material to 100 meshes to obtain nylon fine powder;
[0062] Step B: Hydrolyze the measured dendritic silane-polyamide-amine polymer with 30% distilled water relative to its mass for 2 hours in advance to obtain the coupling agent hydrolysate, and then add the magnetic filler to the temperature-controlled high-speed batching In the mixer, add the above coupling agent hydrolysate, mix at high speed for 10 minutes, after mixing uniformly, adjust the mixer speed to 5r / min, raise the temperature to 100°C, pre-react for 2 hours, and stop the temperature control.
[0063] Step C: Continue to put nylon micropowder and other additives into the high-speed batching mixer described in Step B, and mix at high speed for 10 minutes to obtain a premixed mixtur...
PUM
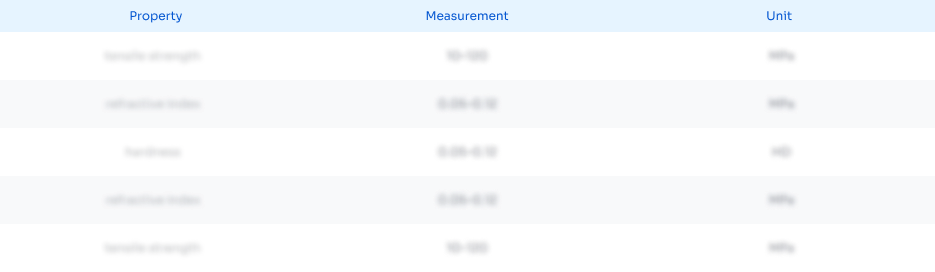
Abstract
Description
Claims
Application Information

- Generate Ideas
- Intellectual Property
- Life Sciences
- Materials
- Tech Scout
- Unparalleled Data Quality
- Higher Quality Content
- 60% Fewer Hallucinations
Browse by: Latest US Patents, China's latest patents, Technical Efficacy Thesaurus, Application Domain, Technology Topic, Popular Technical Reports.
© 2025 PatSnap. All rights reserved.Legal|Privacy policy|Modern Slavery Act Transparency Statement|Sitemap|About US| Contact US: help@patsnap.com