Laser cladding method for valve plate and valve seat in valve
A laser cladding and valve plate technology, which is applied in the coating and metal material coating process, etc., can solve the problems of insufficient bonding force, peeling of the coating and the base material, and the inability of the coating and the base material to form a firm metallurgical bond. , to achieve the effect of strong hardness and wear resistance, increasing the amount of addition
- Summary
- Abstract
- Description
- Claims
- Application Information
AI Technical Summary
Problems solved by technology
Method used
Image
Examples
preparation example Construction
[0039] Step 1. Preparation of semi-finished products: by mechanical processing and other means, the blanks are processed into semi-finished products according to the drawings of the valve plate and valve seat, and the semi-finished products are reserved for the size of the parts that need laser cladding and additives.
[0040] Step 2. Visual inspection or contact inspection: put the semi-finished product into the area to be processed in the laser cladding system and fix it, and then use sensors such as cameras or contact probes to detect the position, length, width, Height, straight and circular hole boundaries.
[0041]Step 3. Path generation: The valve plate is arranged in parallel lines of single-layer multi-lane or multi-layer multi-lane according to plane cladding to generate a walking path for laser cladding; the valve seat generates a path in the form of a ring or a spiral line, and finally cover the entire plane;
[0042] Step 4. Laser cladding: Set the process parame...
Embodiment 1
[0061] This embodiment provides a laser cladding method for a valve plate and a valve seat in a valve, which includes the following steps:
[0062] Step 1. Preparation of semi-finished products: by mechanical processing, according to the drawings of the valve plate and valve seat, the blank is processed into figure 2 , 3 The semi-finished product shown, and the semi-finished product is reserved for the size of the part that needs laser cladding and additives.
[0063] Step 2. Visual inspection or contact inspection: put the semi-finished product into the area to be processed in the laser cladding system and fix it, and then use sensors such as cameras or contact probes to detect the position, length, width, Height, straight and circular hole boundaries.
[0064] Step 3. Path generation: The valve plate is arranged in parallel lines of single-layer multi-lane or multi-layer multi-lane according to plane cladding to generate a walking path for laser cladding; the valve seat g...
Embodiment 1-2~ Embodiment 1-7
[0068] On the basis of Example 1, the ratio of the iron-based powder is adjusted, and its specific ratio and related mechanical performance test data are shown in the table below (wear resistance: at a test pressure of 240N / reciprocating frequency of 2Hz, the test time 2h, detect the amount of wear loss of the cladding layer).
[0069]
PUM
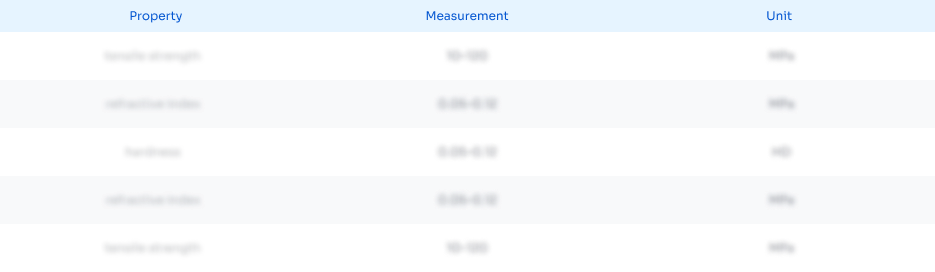
Abstract
Description
Claims
Application Information

- R&D
- Intellectual Property
- Life Sciences
- Materials
- Tech Scout
- Unparalleled Data Quality
- Higher Quality Content
- 60% Fewer Hallucinations
Browse by: Latest US Patents, China's latest patents, Technical Efficacy Thesaurus, Application Domain, Technology Topic, Popular Technical Reports.
© 2025 PatSnap. All rights reserved.Legal|Privacy policy|Modern Slavery Act Transparency Statement|Sitemap|About US| Contact US: help@patsnap.com