Preparation method of epoxy resin and organic silicon composite pouring sealant
A technology of epoxy resin and silicone, which is applied in the field of potting glue, can solve the problems of poor flame retardancy and bonding performance, high rigidity of epoxy resin, poor dimensional stability, etc., and achieve improved oxidation resistance and moderate curing conditions , low-cost effect
- Summary
- Abstract
- Description
- Claims
- Application Information
AI Technical Summary
Problems solved by technology
Method used
Examples
Embodiment 1
[0031] An epoxy resin silicone composite potting glue, which is composed of component A and component B in a weight ratio of 1:1;
[0032] The A component includes the following raw materials in parts by weight: 45 parts of bisphenol A epoxy resin, 10 parts of alumina-coated graphene, 5 parts of epoxy siloxane coupling agent, and 5 parts of dibenzyl phosphate;
[0033] The B component includes the following raw materials in parts by weight: 45 parts of amino silicone oil, 5 parts of aminosilane coupling agent, 10 parts of alumina-coated graphene;
[0034] The preparation method of the alumina-coated graphene comprises the following steps: adding 1000 g of distilled water and 10 g of emulsifier sodium dodecylbenzenesulfonate to 100 g of graphene treated at 280 ° C, and adding dilute hydrochloric acid to adjust the pH of the suspension Value to neutral, and ultrasonic dispersion. After heating to 200°C, slowly add 500 g of aluminum chloride solution with a mass fraction of 10% ...
Embodiment 2
[0042] An epoxy resin silicone composite potting glue, which is composed of component A and component B in a weight ratio of 1:1.2;
[0043] The A component includes the following raw materials in parts by weight: 48 parts of o-cresol novolac epoxy resin, 13 parts of alumina-coated graphene, 7 parts of epoxy siloxane coupling agent, and 7 parts of dibenzyl phosphate;
[0044] The B component includes the following raw materials in parts by weight: 48 parts of amino silicone oil, 7 parts of aminosilane coupling agent, and 13 parts of alumina-coated graphene;
[0045] The preparation method of alumina-coated graphene comprises the following steps: adding 1000 g of distilled water and 20 g of emulsifier polyoxypropylene polyvinyl glyceryl ether to 100 g of graphene treated at 290 ° C, and adding dilute hydrochloric acid to adjust the pH value of the suspension To neutral, and ultrasonic dispersion. After heating to 220°C, slowly add 600g of aluminum chloride solution with a mass...
Embodiment 3
[0053] An epoxy resin silicone composite potting glue, which is composed of component A and component B with a weight ratio of 1:1.7;
[0054] The A component includes the following raw materials in parts by weight: 55 parts of epoxy resin, 17 parts of alumina-coated graphene, 7 parts of epoxy siloxane coupling agent, and 8 parts of dibenzyl phosphate;
[0055] The B component includes the following raw materials in parts by weight: 55 parts of amino silicone oil, 7 parts of aminosilane coupling agent, and 16 parts of alumina-coated graphene;
[0056] The preparation method of alumina-coated graphene comprises the following steps: adding 1000 g of distilled water and 22 g of emulsifier nonylphenol polyoxyethylene ether to 100 g of graphene treated at 285 ° C, adding dilute hydrochloric acid to adjust the pH value of the suspension To neutral, and ultrasonic dispersion. After heating to 240° C., slowly add 700 g of aluminum chloride solution with a mass fraction of 16% into th...
PUM
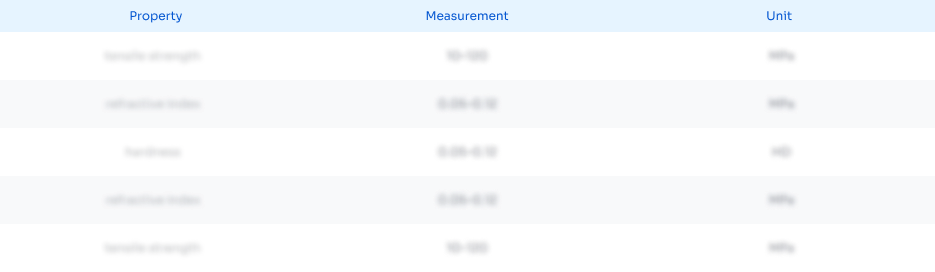
Abstract
Description
Claims
Application Information

- R&D
- Intellectual Property
- Life Sciences
- Materials
- Tech Scout
- Unparalleled Data Quality
- Higher Quality Content
- 60% Fewer Hallucinations
Browse by: Latest US Patents, China's latest patents, Technical Efficacy Thesaurus, Application Domain, Technology Topic, Popular Technical Reports.
© 2025 PatSnap. All rights reserved.Legal|Privacy policy|Modern Slavery Act Transparency Statement|Sitemap|About US| Contact US: help@patsnap.com