Method and system for full gas cooling of secondary cooling section of continuous casting
A secondary cooling and gas cooling technology, which is applied in the field of continuous casting in the metallurgical industry, can solve the problems of poor working environment in the secondary cooling section, reduced metal yield, and uneven surface temperature of the slab, so as to improve the cooling efficiency of continuous casting and Continuous casting slab quality, avoiding slab surface oxidation and uneven cooling, and eliminating the effect of high temperature slab surface oxidation
- Summary
- Abstract
- Description
- Claims
- Application Information
AI Technical Summary
Problems solved by technology
Method used
Image
Examples
Embodiment 1
[0057] refer to figure 2 and image 3 , In this embodiment, a 150×150mm billet with Q235 steel as an example is used to introduce a method and system for full gas cooling in the secondary cooling section of continuous casting.
[0058] The method is as figure 2 As shown, the thick solid line is the cooling gas passage, and the thin solid line is the cooling medium passage. The direction of the suction port is consistent with that of the gas nozzle. The cooling gas is argon, which is sprayed from the gas nozzle to the surface of the slab, and the heat released by the solidification of the slab is taken away by forced convection heat exchange and radiation heat exchange, and then the argon is recovered from the suction port and sent to the cooling equipment It is cooled, and after the temperature of the argon gas drops to 25±5°C, it is sent to the nozzle for recycling. In this embodiment, the cooling medium is water. The arrangement of gas nozzles in this embodiment is sh...
Embodiment 2
[0091] refer to figure 2 and image 3 , In this embodiment, a 280 × 325mm bloom, casting steel 42CrMo, as an example to introduce a method and system of full gas cooling in the secondary cooling section of continuous casting.
[0092] The method is as figure 2 As shown, the thick solid line is the cooling gas passage, and the thin solid line is the cooling medium passage. The direction of the suction port is consistent with that of the nozzle. The cooling gas is argon, which is injected from the nozzle to the surface of the slab, and the heat released by the solidification of the slab is taken away by forced convection heat exchange and radiation heat exchange, and then the argon is recovered from the suction port and sent to the cooling equipment It is cooled, and the argon gas temperature drops to 25±5°C, and then it is sent to the nozzle for recycling. In this embodiment, the cooling medium is water. The arrangement of gas nozzles in this embodiment is shown in ima...
Embodiment 3
[0125] refer to figure 2 and image 3 , in this embodiment, a 220 × 1800mm slab, cast steel as Q235B, as an example to introduce a method and system of full gas cooling in the secondary cooling section of continuous casting.
[0126] The method is as figure 2 As shown, the thick solid line is the cooling gas passage, and the thin solid line is the cooling medium passage. The direction of the suction port is consistent with that of the gas nozzle. The cooling gas is argon, which is injected from the gas nozzle to the surface of the slab, and the heat released by the solidification of the slab is taken away by forced convection heat exchange and radiation heat exchange, and then the argon is recovered by the suction port and sent to the cooling equipment It is cooled, and after the temperature of the argon gas drops to 25±5°C, it is sent to the gas nozzle for recycling. In this embodiment, the cooling medium is water. The top view of the arrangement of gas nozzles in this...
PUM
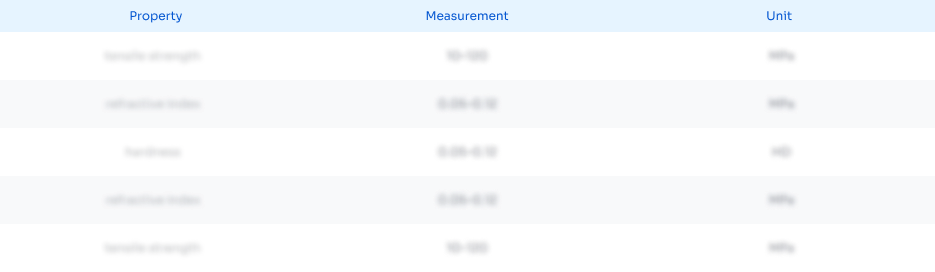
Abstract
Description
Claims
Application Information

- R&D
- Intellectual Property
- Life Sciences
- Materials
- Tech Scout
- Unparalleled Data Quality
- Higher Quality Content
- 60% Fewer Hallucinations
Browse by: Latest US Patents, China's latest patents, Technical Efficacy Thesaurus, Application Domain, Technology Topic, Popular Technical Reports.
© 2025 PatSnap. All rights reserved.Legal|Privacy policy|Modern Slavery Act Transparency Statement|Sitemap|About US| Contact US: help@patsnap.com