System for producing high-whiteness calcined kaolin by multistage suspension calcination of coal series kaolin
A technology of coal series kaolin and calcined kaolin, applied in the direction of inorganic chemistry, non-metallic elements, silicon compounds, etc., can solve the problems of poor quality uniformity, low processing capacity, low heat utilization rate, etc., and achieve low processing cost and low energy consumption , High heat and mass transfer efficiency
- Summary
- Abstract
- Description
- Claims
- Application Information
AI Technical Summary
Problems solved by technology
Method used
Image
Examples
Embodiment 1
[0047] The system structure of multi-stage suspension calcination of coal series kaolin to produce high whiteness calcined kaolin is as follows: figure 1 As shown, it includes a crusher 1, a mill 2, a feeding bin 4, a screw feeder 6, a suspension dehydration calciner 7, a first cyclone separator 8, a suspension dehydration calciner 9, a second cyclone separator 10, Suspension decarburization calciner 11, third cyclone separator 12, primary cooler 13 and secondary cooler 14;
[0048] The discharge port of the crusher 1 is opposite to the feed port of the mill 2, the discharge port of the mill 2 is opposite to the first feeding belt 3, and the discharge end of the first feeding belt 3 is matched with the feeding bin 4; The discharge port of the feed bin 4 is opposite to the second feed belt 5, the second feed belt 5 matches the feed end of the screw feeder 6, and the discharge end of the screw feeder 6 is connected to the top of the suspension dehydration calciner 7 The feed po...
Embodiment 2
[0068] System structure is the same as embodiment 1;
[0069] Method is with embodiment 1, and difference is:
[0070] (1) Particle size ≤ 0.002mm in the powder accounts for 92% of the total mass; coal series kaolin contains SiO by mass percentage 2 43.55%, Al 2 o 3 38.11%, Fe 2 o 3 0.21%, CaO 0.47%, TiO 2 0.16%, MgO 0.23%, K 2 O0.31%, Na 2 O 0.22%, C 1.51%;
[0071] (2) Dehydration reaction is carried out at 250°C; the residence time of the powder in the suspension dehydration calciner is 6min;
[0072] (3) Dehydration reaction at 800°C; the residence time of the dehydrated material in the suspension dehydroxylation calciner is 20min;
[0073] (4) Decarburization reaction is carried out at 900°C, the volume flow ratio of air and nitrogen is 1:1.5; the residence time of the dehydroxylation material in the suspension decarburization calciner is 60min;
[0074] (5) After the countercurrent heat exchange between the decarbonized material and the air, the temperature o...
Embodiment 3
[0077] System structure is the same as embodiment 1;
[0078] Method is with embodiment 1, and difference is:
[0079] (1) Particle size ≤ 0.002mm in the powder accounts for 95% of the total mass; coal series kaolin contains SiO in mass percentage 2 45.16%, Al 2 o 3 36.54%, Fe 2 o 3 0.16%, CaO 0.55%, TiO 2 0.38%, MgO 0.4%, K 2 O0.36%, Na 2 O 0.35%, C 1.3%;
[0080] (2) Dehydration reaction is carried out at 300°C; the residence time of the powder in the suspension dehydration calciner is 2min;
[0081] (3) Dehydration reaction at 900°C; the residence time of the dehydrated material in the suspension dehydroxylation calciner is 10 minutes;
[0082] (4) Decarburization reaction is carried out at 950°C, the volume flow ratio of air and nitrogen is 1:2; the residence time of the dehydration material in the suspension decarburization calciner is 40min;
[0083] (5) After the countercurrent heat exchange between the decarbonized material and the air, the temperature of...
PUM
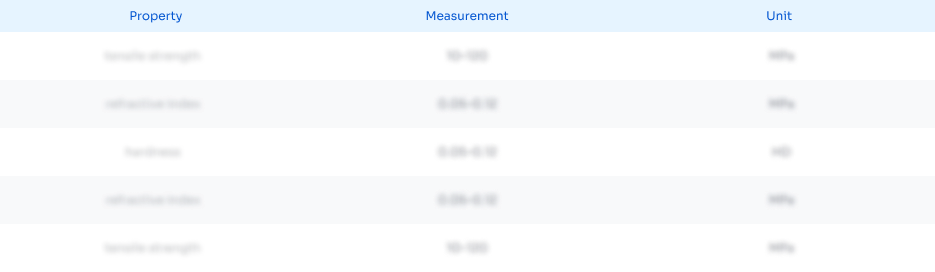
Abstract
Description
Claims
Application Information

- R&D Engineer
- R&D Manager
- IP Professional
- Industry Leading Data Capabilities
- Powerful AI technology
- Patent DNA Extraction
Browse by: Latest US Patents, China's latest patents, Technical Efficacy Thesaurus, Application Domain, Technology Topic, Popular Technical Reports.
© 2024 PatSnap. All rights reserved.Legal|Privacy policy|Modern Slavery Act Transparency Statement|Sitemap|About US| Contact US: help@patsnap.com