Automobile control panel IMD injection molding process
A technology of automobile control and process, which is applied in the field of IMD injection molding process of automobile control panel, can solve the problems of difficult color control, large color difference, high processing defect rate, etc., and achieve the goal of improving economic and environmental benefits, reducing air bubbles, and increasing injection molding yield Effect
- Summary
- Abstract
- Description
- Claims
- Application Information
AI Technical Summary
Problems solved by technology
Method used
Image
Examples
Embodiment 1
[0029] see figure 1 , the present invention provides a kind of technical scheme: a kind of automobile control panel IMD injection molding process, comprises the following steps:
[0030] Step 1: Cut PVC or PET sheets;
[0031] Step 2: The cut sheet is placed in a 100,000-level purification workshop for purification; a 100,000-level purification workshop means that the particles per cubic meter in the workshop are controlled within 10W;
[0032] Step 3: After purification, take out the sheet and place it in a dryer for baking at 90°C for 2 hours;
[0033] Step 4: After baking, use light-curable ink to screen-print the sheet. The mesh number of the screen is 120 mesh / cm monofilament polyester screen; screen printing can be automated, with high production efficiency and UV ink light. Curing only takes a few seconds or more than ten seconds. The curing speed is very fast, and finer lines can be screen printed. The resolution is high, and the ink layer is thinner, and the printin...
Embodiment 2
[0040] see figure 1 , the present invention provides a kind of technical scheme: a kind of automobile control panel IMD injection molding process, comprises the following steps:
[0041] Step 1: Cut PVC or PET sheets;
[0042] Step 2: The cut sheet is placed in a 100,000-level purification workshop for purification; a 100,000-level purification workshop means that the particles per cubic meter in the workshop are controlled within 10W;
[0043] Step 3: After purification, take out the sheet and place it in a dryer for 1.5 hours at 105°C;
[0044] Step 4: After baking, use light-curable ink to screen-print the sheet. The mesh number of the screen is 143 mesh / cm monofilament polyester screen; screen printing can be automated, with high production efficiency and UV ink light. Curing only takes a few seconds or more than ten seconds. The curing speed is very fast, and finer lines can be screen printed. The resolution is high, and the ink layer is thinner, and the printing area i...
Embodiment 3
[0051] see figure 1 , the present invention provides a kind of technical scheme: a kind of automobile control panel IMD injection molding process, comprises the following steps:
[0052] Step 1: Cut PVC or PET sheets;
[0053] Step 2: The cut sheet is placed in a 100,000-level purification workshop for purification; a 100,000-level purification workshop means that the particles per cubic meter in the workshop are controlled within 10W;
[0054] Step 3: After purification, take out the sheet and place it in a dryer for baking at 120°C for 1 hour;
[0055] Step 4: After baking, use light-curable ink to screen-print the sheet. The mesh number of the screen is 165 mesh / cm monofilament polyester screen; screen printing can be automated, with high production efficiency and UV ink light. Curing only takes a few seconds or more than ten seconds. The curing speed is very fast, and finer lines can be screen printed. The resolution is high, and the ink layer is thinner, and the printin...
PUM
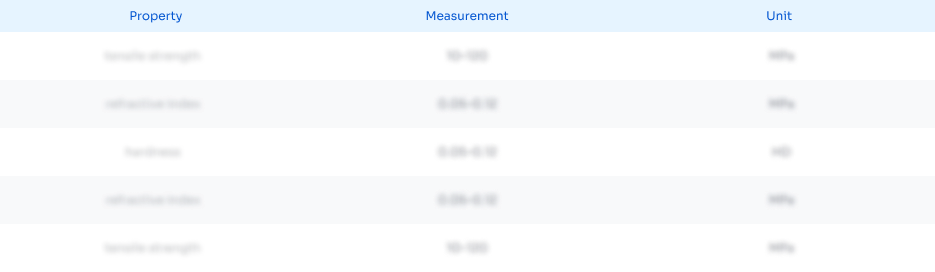
Abstract
Description
Claims
Application Information

- R&D Engineer
- R&D Manager
- IP Professional
- Industry Leading Data Capabilities
- Powerful AI technology
- Patent DNA Extraction
Browse by: Latest US Patents, China's latest patents, Technical Efficacy Thesaurus, Application Domain, Technology Topic, Popular Technical Reports.
© 2024 PatSnap. All rights reserved.Legal|Privacy policy|Modern Slavery Act Transparency Statement|Sitemap|About US| Contact US: help@patsnap.com