Manufacturing process of two-step plate
A manufacturing process and step plate technology, applied in multilayer circuit manufacturing, printed circuit manufacturing, electrical components, etc., can solve problems such as reducing glue flow and abnormal quality
- Summary
- Abstract
- Description
- Claims
- Application Information
AI Technical Summary
Problems solved by technology
Method used
Examples
Embodiment
[0027] This embodiment provides a manufacturing process of a twice-stepped plate, one side of the twice-stepped plate is provided with a stepped groove with a large outside and a small inside, and the specific process is as follows:
[0028] (1) Cutting: Cut out the first core board, the second core board, the first non-flowing PP and the second non-flowing PP according to the panel size 467mm×620mm, and the thickness of the first core board is 2.93mm ( The thickness is the thickness without the outer copper foil), the thickness of the outer copper foil is 1oz; the thickness of the second core board is 0.865mm (the thickness is the thickness without the outer copper foil), the thickness of the outer copper foil is 0.5OZ.
[0029] (2) Micro-etching: paste a dry film on one of the surfaces of the first core board, and then etch the outer layer copper foil on the surface to a thickness of 0.5 oz through micro-etching, so as to facilitate the later production of the outer layer ci...
PUM
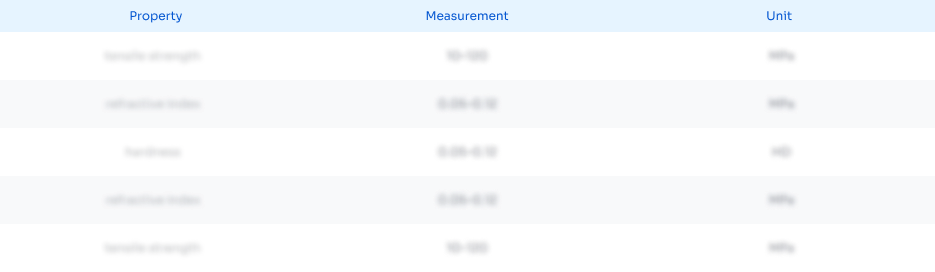
Abstract
Description
Claims
Application Information

- Generate Ideas
- Intellectual Property
- Life Sciences
- Materials
- Tech Scout
- Unparalleled Data Quality
- Higher Quality Content
- 60% Fewer Hallucinations
Browse by: Latest US Patents, China's latest patents, Technical Efficacy Thesaurus, Application Domain, Technology Topic, Popular Technical Reports.
© 2025 PatSnap. All rights reserved.Legal|Privacy policy|Modern Slavery Act Transparency Statement|Sitemap|About US| Contact US: help@patsnap.com