High-strength porous water permeable brick and preparation method thereof
A high-strength, permeable brick technology, applied in the direction of manufacturing tools, clay products, ceramic products, etc., can solve the problems that the ground is not easy to dry, affects the water permeability of the brick body, and is easy to reverse osmosis, etc.
- Summary
- Abstract
- Description
- Claims
- Application Information
AI Technical Summary
Problems solved by technology
Method used
Examples
Embodiment 1
[0024] 1. Coal slag carbon reduction treatment:
[0025] a. adding water to quicklime and stirring it, leaving it to stand for stratification, taking off the suspension in the lower layer and vacuum-drying until the water content is 45%, so as to obtain milk of lime;
[0026] b. Activation: Grind the coal slag, add 1.5% sodium sulfate after magnetic separation, mix and grind it with milk of lime of the same quality as the coal slag, filter out the oozing water during the process, and roast at 150°C for 1.5h , crushed after cooling.
[0027] 2. Shale modification:
[0028] a. Crush the shale into coarse grains with a particle size of 4 mm, calcining at 90°C for 80 minutes, taking it out, calcining at 230°C for 15 minutes, and then calcining at 160°C for 35 minutes;
[0029] b. When the calcined shale coarse grains are cooled to 70°C, hydrogen peroxide is added dropwise, and when no air bubbles appear, the shale coarse grains are dried and pulverized for grinding to obtain mod...
Embodiment 2
[0037] Specifically, it is realized through the following technical solutions:
[0038] 1. Coal slag carbon reduction treatment:
[0039] a. add quicklime to water and stir, then let it stand for stratification, take off the lower layer of suspension and vacuum-dry until the water content is 50%, to obtain milk of lime;
[0040] b. Activation: Crush the cinder, add 2% sodium sulfate after magnetic separation, then mix and grind it with milk of lime of the same quality as the cinder, filter out the oozing water during the process, and roast at 170°C for 1 hour. After cooling, crush it.
[0041] 2. Shale modification:
[0042] a. Crush the shale into coarse particles with a particle size of 5 mm, calcining at 110°C for 65 minutes, taking it out, calcining at 240°C for 10 minutes, and then calcining at 170°C for 30 minutes;
[0043]b. When the calcined shale coarse grains are cooled to 80°C, hydrogen peroxide is added dropwise, and when no air bubbles appear, the shale coarse ...
Embodiment 3
[0051] Specifically, it is realized through the following technical solutions:
[0052] 1. Coal slag carbon reduction treatment:
[0053] a. add quicklime to water and stir, then let it stand for stratification, take off the suspension in the lower layer and vacuum-dry until the water content is 40%, to obtain milk of lime;
[0054] b. Activation: Crush the cinder, add 1% sodium sulfate after magnetic separation, mix and grind it with milk of lime of the same quality as the cinder, filter out the oozing water during the process, and roast at 130°C for 2 hours. After cooling, crush it.
[0055] 2. Shale modification:
[0056] a. Crush the shale into coarse particles with a particle size of 2 mm, calcining at 70°C for 90 minutes, taking it out, calcining at 220°C for 20 minutes, and then calcining at 150°C for 30 minutes;
[0057] b. When the calcined shale coarse grains are cooled to 60°C, hydrogen peroxide is added dropwise until no air bubbles appear, then the shale coarse...
PUM
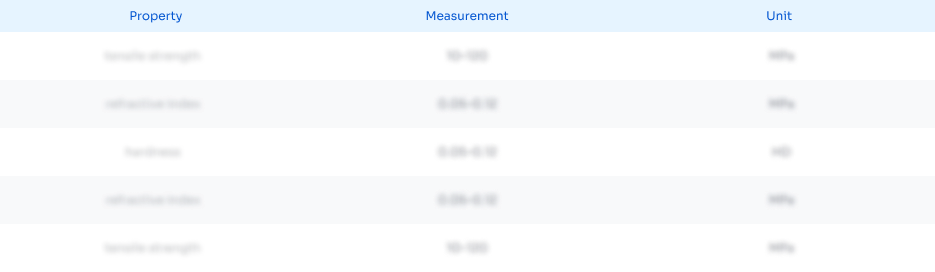
Abstract
Description
Claims
Application Information

- R&D
- Intellectual Property
- Life Sciences
- Materials
- Tech Scout
- Unparalleled Data Quality
- Higher Quality Content
- 60% Fewer Hallucinations
Browse by: Latest US Patents, China's latest patents, Technical Efficacy Thesaurus, Application Domain, Technology Topic, Popular Technical Reports.
© 2025 PatSnap. All rights reserved.Legal|Privacy policy|Modern Slavery Act Transparency Statement|Sitemap|About US| Contact US: help@patsnap.com