Surface finish machining treatment system and treatment process after casting molding of casting part
A casting molding and processing system technology, used in manufacturing tools, metal processing equipment, grinding workpiece supports, etc., can solve the problems of inability to grind multiple wrenches, low grinding efficiency, and high labor intensity
- Summary
- Abstract
- Description
- Claims
- Application Information
AI Technical Summary
Problems solved by technology
Method used
Image
Examples
Embodiment Construction
[0027] The embodiments of the present invention will be described in detail below with reference to the accompanying drawings, but the present invention can be implemented in many different ways defined and covered by the claims.
[0028] Such as Figure 1 to Figure 6 As shown, a casting surface finishing treatment system after pouring molding, including a support frame 1, a clamping device 2, a grinding device 3 and a cleaning device 4, the middle part of the support frame 1 is provided with a clamping device 2 and a cleaning device 4. The cleaning device 4 is located above the clamping device 2, and the grinding device 3 is symmetrically installed on the left and right ends of the support frame 1.
[0029] The middle part of the support frame 1 is equipped with a collection box 11 for collecting workpieces by sliding fit, and a filter screen is arranged in the collection box 11. During specific work, the left and right sides of the collection box 11 are provided with a colle...
PUM
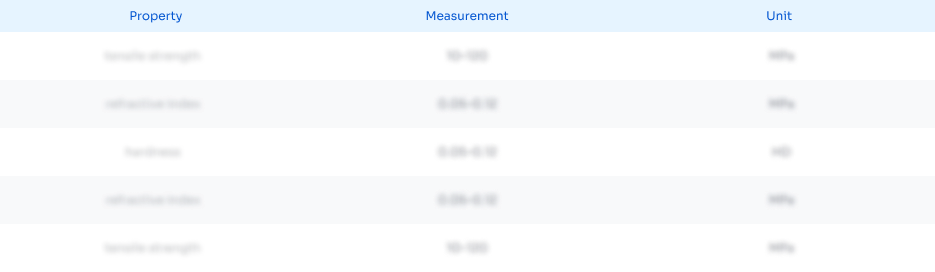
Abstract
Description
Claims
Application Information

- Generate Ideas
- Intellectual Property
- Life Sciences
- Materials
- Tech Scout
- Unparalleled Data Quality
- Higher Quality Content
- 60% Fewer Hallucinations
Browse by: Latest US Patents, China's latest patents, Technical Efficacy Thesaurus, Application Domain, Technology Topic, Popular Technical Reports.
© 2025 PatSnap. All rights reserved.Legal|Privacy policy|Modern Slavery Act Transparency Statement|Sitemap|About US| Contact US: help@patsnap.com