Stainless steel passivation agent and preparation method thereof
A passivating agent, stainless steel technology, applied in the direction of metal material coating process, etc., can solve the problems of unfavorable sustainable development, environmental pollution, etc., to achieve the effect of protection from corrosion and prolonging service life
- Summary
- Abstract
- Description
- Claims
- Application Information
AI Technical Summary
Problems solved by technology
Method used
Examples
Embodiment 1
[0020] A stainless steel passivator, consisting of the following components:
[0021] Citric Acid 10%
[0022] Phytic Acid 5%
[0023] Dicumyl peroxide 2%
[0024] Waterborne Acrylic Polysiloxane 3%
[0025] Tetrasodium iminodisuccinate 0.3%
[0026] The balance is deionized water
[0027] A stainless steel passivator is prepared by the following method: according to the above ratio, citric acid, phytic acid, dicumyl peroxide, tetrasodium iminodisuccinate and water-based acrylic polysiloxane are added to deionized In water, heat up to 50°C and stir for 20 minutes to form a passivating agent.
[0028] The stainless steel workpiece was cleaned with deionized water, polished and decontaminated with sandpaper, then ultrasonically cleaned in ethanol solution, then cleaned in hydrochloric acid solution to remove the surface oxide film, and finally rinsed with deionized water. First heat the prepared passivating agent to 50°C, put the pretreated stainless steel workpiece into t...
Embodiment 2
[0030] A stainless steel passivator, consisting of the following components:
[0031] Citric Acid 12%
[0032] Phytic Acid 6%
[0033] Dicumyl peroxide 3%
[0034] Waterborne Acrylic Polysiloxane 5%
[0035] Sodium iminodisuccinate 0.4%
[0036] The balance is deionized water
[0037] A stainless steel passivator is prepared by the following method:
[0038] According to the above ratio, add citric acid, phytic acid, dicumyl peroxide, tetrasodium iminodisuccinate and aqueous acrylic polysiloxane into deionized water, raise the temperature to 50°C, and stir for 20 minutes to form passivation agent.
[0039] The stainless steel workpiece was cleaned with deionized water, polished and decontaminated with sandpaper, then ultrasonically cleaned in ethanol solution, then cleaned in hydrochloric acid solution to remove the surface oxide film, and finally rinsed with deionized water. First heat the prepared passivating agent to 50°C, put the pretreated stainless steel workpiece...
Embodiment 3
[0041] A stainless steel passivator, consisting of the following components:
[0042] Citric Acid 14%
[0043] Phytic Acid 8%
[0044] Dicumyl peroxide 4%
[0045] Waterborne Acrylic Polysiloxane 6%
[0046] Tetrasodium iminodisuccinate 0.5%
[0047] The balance is deionized water
[0048] A stainless steel passivator is prepared by the following method:
[0049] According to the above ratio, add citric acid, phytic acid, dicumyl peroxide, tetrasodium iminodisuccinate and aqueous acrylic polysiloxane into deionized water, raise the temperature to 50°C, and stir for 20 minutes to form passivation agent.
[0050] The stainless steel workpiece was cleaned with deionized water, polished and decontaminated with sandpaper, then ultrasonically cleaned in ethanol solution, then cleaned in hydrochloric acid solution to remove the surface oxide film, and finally rinsed with deionized water. First heat the prepared passivating agent to 50°C, put the pretreated stainless steel work...
PUM
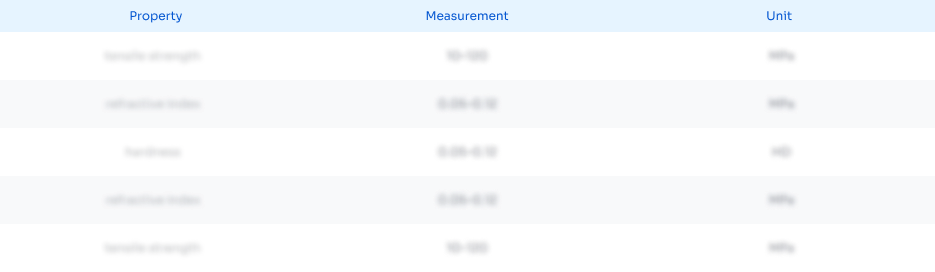
Abstract
Description
Claims
Application Information

- Generate Ideas
- Intellectual Property
- Life Sciences
- Materials
- Tech Scout
- Unparalleled Data Quality
- Higher Quality Content
- 60% Fewer Hallucinations
Browse by: Latest US Patents, China's latest patents, Technical Efficacy Thesaurus, Application Domain, Technology Topic, Popular Technical Reports.
© 2025 PatSnap. All rights reserved.Legal|Privacy policy|Modern Slavery Act Transparency Statement|Sitemap|About US| Contact US: help@patsnap.com