Method for preparing nitrogen-doped MnCr2O4 coating on surface of FeCrNi alloy
A technology of nitrogen doping and alloying, which is applied in the direction of metal material coating process, coating, solid-state diffusion coating, etc., can solve the problems of limited anti-coking carburization performance and low content, so as to improve anti-coking carburization performance, The effect of suppressing catalytic coking
- Summary
- Abstract
- Description
- Claims
- Application Information
AI Technical Summary
Problems solved by technology
Method used
Image
Examples
Embodiment 1
[0038] (1) Manganese sulfate, chromium chloride, ammonium sulfate, ammonium citrate, sodium lauryl sulfate, sodium oxalate and formic acid are dissolved in distilled water to form a plating solution. The concentration of each component in the plating solution is: manganese sulfate 100g / L, chromium chloride 150g / L, ammonium sulfate 100g / L, ammonium citrate 25g / L, sodium lauryl sulfate 0.8g / L, sodium oxalate 20g / L, formic acid 20g / L;
[0039] (2) FeCrNi alloy is used as the substrate, and the metal coating is formed by pulse electrodeposition in the plating solution (the coating consists of metal Mn, metal Cr and a small amount of MnCr alloy). The specific electrodeposition process is as follows: use platinum electrode as anode, FeCrNi alloy as cathode, use dilute sulfuric acid and dilute sodium hydroxide solution to adjust the pH value of the plating solution to 3.5, the temperature of the plating solution is 25°C, and use electromagnetic stirring during the electroplating proce...
Embodiment 2
[0045] (1) Manganese sulfate, chromium chloride, ammonium sulfate, ammonium citrate, sodium lauryl sulfate, sodium oxalate and formic acid are dissolved in distilled water to form a plating solution. The concentration of each component in the plating solution is: manganese sulfate 100g / L, chromium chloride 150g / L, ammonium sulfate 100g / L, ammonium citrate 25g / L, sodium lauryl sulfate 0.8g / L, sodium oxalate 20g / L, formic acid 20g / L;
[0046] (2) FeCrNi alloy is used as the substrate, and the metal coating is formed by pulse electrodeposition in the plating solution (the coating consists of metal Mn, metal Cr and a small amount of MnCr alloy). The specific electrodeposition process is as follows: use platinum electrode as anode, FeCrNi alloy as cathode, use dilute sulfuric acid and dilute sodium hydroxide solution to adjust the pH value of the plating solution to 3.5, the temperature of the plating solution is 25°C, and use electromagnetic stirring during the electroplating proce...
PUM
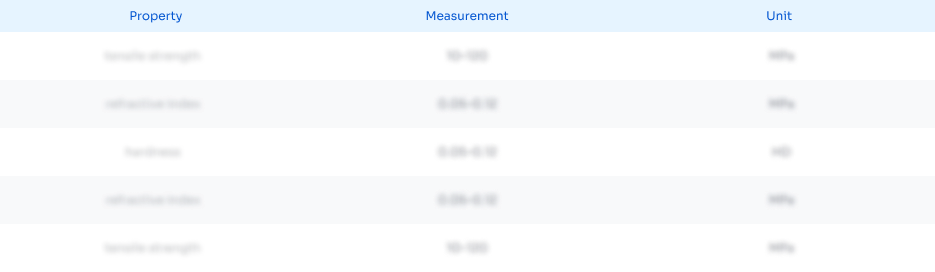
Abstract
Description
Claims
Application Information

- Generate Ideas
- Intellectual Property
- Life Sciences
- Materials
- Tech Scout
- Unparalleled Data Quality
- Higher Quality Content
- 60% Fewer Hallucinations
Browse by: Latest US Patents, China's latest patents, Technical Efficacy Thesaurus, Application Domain, Technology Topic, Popular Technical Reports.
© 2025 PatSnap. All rights reserved.Legal|Privacy policy|Modern Slavery Act Transparency Statement|Sitemap|About US| Contact US: help@patsnap.com