Multifunctional environment-friendly silk-screen transfer printing ink
A technology of cyclohexanone and main resin, which is applied in the field of multi-functional environmental protection screen printing pad printing ink and its preparation, can solve the problem that it is not suitable for screen printing, pad printing or suitable materials, resin malonate ether acetate does not comply with environmental protection regulations, prohibited Substances that do not meet the requirements of environmental protection regulations, etc.
- Summary
- Abstract
- Description
- Claims
- Application Information
AI Technical Summary
Problems solved by technology
Method used
Image
Examples
Embodiment 1
[0034]Prepare a frequency conversion speed regulating stirring and dispersing machine and a 1.5L stainless steel container, take 100g of isophorone, 220g of dibasic ester (DBE), and 200g of cyclohexanone into the container, start the mixer, and adjust the speed to 100 rpm. Slowly add 360g of polyester resin (molecular weight: 19000, Tg: 60), adjust the speed of the mixer to 600 rpm, and stir for 20 minutes. Adjust the speed of the mixer to 1500 rpm. If the temperature in the container exceeds 80°C, the speed of the mixer can be further reduced. The temperature of the container during the whole process does not exceed 80°C. After stirring for 2 hours, visually check whether there is any unmelted resin block in the container. If there is no resin liquid fineness with a scraper fineness meter, if there is no melted resin in the container, continue stirring until it is completely melted Finally, after passing the test with a scraper fineness meter, add 120 g of butyl oxalate aceta...
Embodiment 2
[0036] Prepare a frequency conversion speed regulating stirring dispersing machine and a 1.5L stainless steel container, take 90g of isophorone, 200g of dibasic ester (DBE), and 190g of cyclohexanone into the container, start the mixer, and adjust the speed to 100 rpm. Slowly add 370g of polyester resin (molecular weight: 18000, Tg: 72), adjust the speed of the mixer to 600 rpm, and stir for 20 minutes. Adjust the speed of the mixer to 1500 rpm. If the temperature in the container exceeds 80°C, the speed of the mixer can be further reduced. The temperature of the container during the whole process does not exceed 80°C. After stirring for 2 hours, visually check whether there is any unmelted resin block in the container. If there is no resin liquid fineness with a scraper fineness meter, if there is no melted resin in the container, continue stirring until it is completely melted Finally, after passing the test with a scraper fineness meter, add 150 g of butyl oxalate acetate (...
Embodiment 3
[0038] Prepare a frequency conversion speed regulating stirring dispersing machine and a 1.5L stainless steel container, take 80g of isophorone, 190g of dibasic ester (DBE), and 180g of cyclohexanone into the container, start the mixer, and adjust the speed to 100 rpm. Slowly add 380g of polyester resin (molecular weight: 15000, Tg: 80), adjust the speed of the mixer to 600 rpm, and stir for 20 minutes. Adjust the speed of the mixer to 1500 rpm. If the temperature in the container exceeds 80°C, the speed of the mixer can be further reduced. The temperature of the container during the whole process does not exceed 80°C. After stirring for 2 hours, visually check whether there is any unmelted resin block in the container. If there is no resin liquid fineness with a scraper fineness meter, if there is no melted resin in the container, continue stirring until it is completely melted Finally, after passing the test with a scraper fineness meter, 170 g of butyl oxalate acetate (DBGA...
PUM
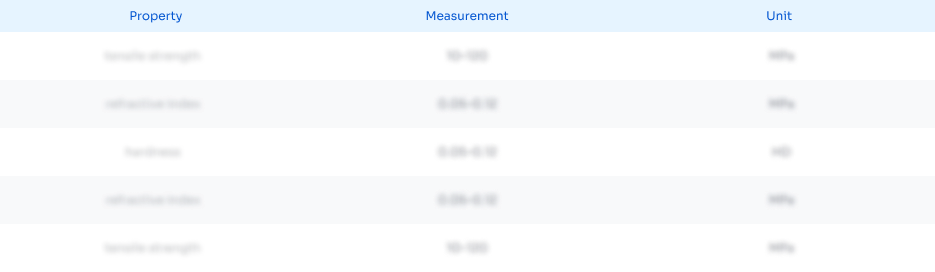
Abstract
Description
Claims
Application Information

- Generate Ideas
- Intellectual Property
- Life Sciences
- Materials
- Tech Scout
- Unparalleled Data Quality
- Higher Quality Content
- 60% Fewer Hallucinations
Browse by: Latest US Patents, China's latest patents, Technical Efficacy Thesaurus, Application Domain, Technology Topic, Popular Technical Reports.
© 2025 PatSnap. All rights reserved.Legal|Privacy policy|Modern Slavery Act Transparency Statement|Sitemap|About US| Contact US: help@patsnap.com