Self-stabilizing ship gangway ladder system and control method
A self-stabilizing, gangway technology, applied in the direction of attitude control, ship accessories, non-electric variable control, etc., can solve the problems of personnel safety injury, lack of electronic and hydraulic assistance, and inability to realize ship attitude collection, etc., to achieve reliable and stable links, The effect of ensuring safe passage
- Summary
- Abstract
- Description
- Claims
- Application Information
AI Technical Summary
Problems solved by technology
Method used
Image
Examples
Embodiment Construction
[0041] The specific embodiment of the present invention will be further described below in conjunction with accompanying drawing and specific embodiment:
[0042] combine Figure 1-Figure 4, Self-stabilized ship gangway system, including six degrees of freedom hydraulic stability platform, gangway stability controller and gangway lifting and rotating mechanism, hydraulic station, gangway walking channel lifting platform, hydraulic station including servo motor, hydraulic pump, proportional solenoid valve , reversing solenoid valve, hydraulic oil tank, mechanical oil level gauge, oil pressure gauge, hydraulic pipeline; the lifting platform of the gangway walking passage includes steel wire rope and drum, gangway walking passage, passage and drum support mechanism and fixed pulley block .
[0043] The six-degree-of-freedom hydraulic stable platform includes a platform stabilization system. The platform stabilization system includes a hydraulic cylinder jacking system and a carr...
PUM
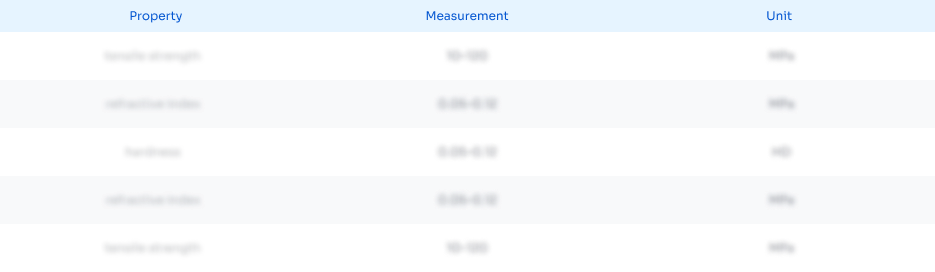
Abstract
Description
Claims
Application Information

- R&D
- Intellectual Property
- Life Sciences
- Materials
- Tech Scout
- Unparalleled Data Quality
- Higher Quality Content
- 60% Fewer Hallucinations
Browse by: Latest US Patents, China's latest patents, Technical Efficacy Thesaurus, Application Domain, Technology Topic, Popular Technical Reports.
© 2025 PatSnap. All rights reserved.Legal|Privacy policy|Modern Slavery Act Transparency Statement|Sitemap|About US| Contact US: help@patsnap.com