Polycrystalline silicon ingot furnace
A polysilicon ingot casting furnace and furnace body technology, which is applied in the directions of polycrystalline material growth, single crystal growth, single crystal growth, etc., can solve the problem that the fixed heat insulation block is difficult to meet, and achieve heat preservation, avoid overheating and melting, and reduce heat loss effect
- Summary
- Abstract
- Description
- Claims
- Application Information
AI Technical Summary
Problems solved by technology
Method used
Image
Examples
Embodiment approach
[0024] In the semi-melting high-efficiency polycrystalline ingot casting process, the crystalline silicon scrap is laid on the bottom of the quartz crucible as the seed crystal when charging. In the melting stage, the silicon material cannot be completely melted, and it is necessary to ensure a certain height of the seed crystal retention layer at the bottom. . Therefore, the first embodiment of the heat insulating block 5 is as follows: during the heating stage, the furnace temperature needs to be raised rapidly, the first hinge 14 and the second hinge 15 are in a horizontal state, and the heat insulating block 5 is placed horizontally, as figure 1 shown. The ingot furnace is divided into upper and lower areas. The area above the insulation block 5 including the top heater 1 and the side heater 2 is the hot area, and the area below the insulation block 5 including the directional heat dissipation block 11 and the water wall 12 of the furnace shell is the cold area. Since th...
Embodiment 2
[0028] During the high-efficiency full-melt polycrystalline ingot casting process, amorphous silicon / silicon-containing materials are fixed at the bottom of the quartz crucible to form a nucleation layer with a rough surface. After the silicon material is completely melted, the erosion time and intensity of the silicon melt to the nucleation layer are controlled. During crystal growth, it is necessary to control the degree of supercooling to grow high-quality polysilicon ingots. Therefore, the second embodiment of the heat insulating block 5 is as follows: during the heating stage, the furnace temperature needs to be raised rapidly, the heat insulating block 5 is placed horizontally, and the first hinge 14 and the second hinge 15 are in a horizontal state, such as figure 1 shown. The ingot furnace is divided into upper and lower areas. The area above the insulation block 5 including the top heater 1 and the side heater 2 is the hot area, and the area below the insulation blo...
PUM
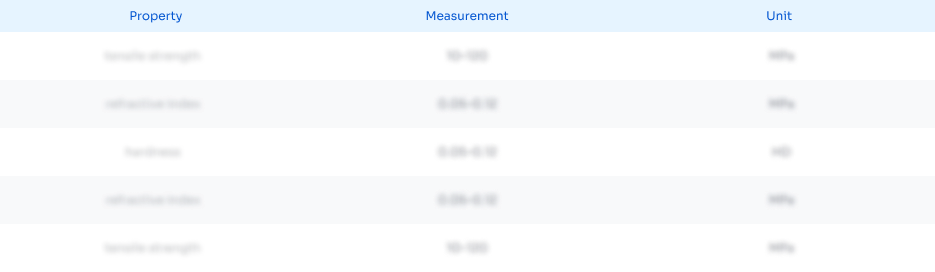
Abstract
Description
Claims
Application Information

- R&D Engineer
- R&D Manager
- IP Professional
- Industry Leading Data Capabilities
- Powerful AI technology
- Patent DNA Extraction
Browse by: Latest US Patents, China's latest patents, Technical Efficacy Thesaurus, Application Domain, Technology Topic, Popular Technical Reports.
© 2024 PatSnap. All rights reserved.Legal|Privacy policy|Modern Slavery Act Transparency Statement|Sitemap|About US| Contact US: help@patsnap.com