Method for producing carbon black by blending biological tar
A technology for producing carbon black and tar, applied in coking ovens, petroleum industry, coking carbon-containing materials, etc., can solve the problems of system energy supply not being considered, high cost of plasma operation and maintenance, low probability, etc., to achieve process operability and applicability, enhanced cycle performance and mechanical strength, and reduced energy and material consumption
- Summary
- Abstract
- Description
- Claims
- Application Information
AI Technical Summary
Problems solved by technology
Method used
Image
Examples
Embodiment 1
[0034] A strontium nitrate solution with a concentration of 10% and an aluminum nitrate solution with a concentration of 5% were mixed at room temperature, then spray-dried at 180°C, and the solid mixture formed was roasted at 1200°C for 6 hours to obtain a powdery heat carrier. In terms of mass percentage, CO 2 The absorption component is 70%, the carrier is 30%, and then the molded heat carrier CA-1 with a particle size of 0.2mm is prepared on a rotary tablet press under a pressure of 10KN.
Embodiment 2
[0036] Weigh strontium nitrate, magnesium nitrate and calcium nitrate according to the mass ratio of 1:0.03:0.015 and mix them to prepare an absorption component precursor solution with a concentration of 10%, and weigh aluminum nitrate and zirconium nitrate according to the mass ratio of 1:0.1 and mix them And prepare a support body precursor solution with a concentration of 5%, mix the two precursor solutions at room temperature, then spray dry at 220°C, and bake the formed solid mixture at 1200°C for 6 hours to obtain a powdery heat carrier , in terms of mass percentage, CO 2 The absorption component is 70%, the carrier is 30%, and then the molded heat carrier CA-2 with a particle size of 0.2mm is prepared on a rotary tablet press under a pressure of 10KN.
Embodiment 3
[0038] Weigh strontium nitrate, magnesium nitrate and calcium nitrate according to the mass ratio of 1:0.15:0.075 and mix them to prepare an absorption component precursor solution with a concentration of 10%, and weigh aluminum nitrate and zirconium nitrate according to the mass ratio of 1:1 and mix them And prepare a support body precursor solution with a concentration of 5%, mix the two precursor solutions at room temperature, and then spray dry at 260°C, and bake the formed solid mixture at 1400°C for 4 hours to obtain a powdery heat carrier , in terms of mass percentage, CO 2 The absorption component is 60%, the carrier is 40%, and then the molded heat carrier CA-3 with a particle size of 0.5mm is prepared on a rotary tablet press under a pressure of 10KN.
PUM
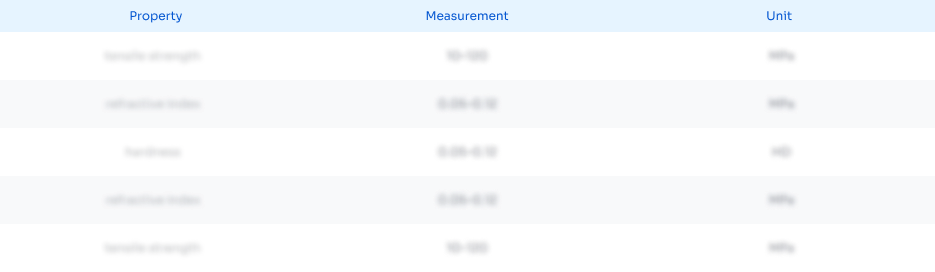
Abstract
Description
Claims
Application Information

- R&D Engineer
- R&D Manager
- IP Professional
- Industry Leading Data Capabilities
- Powerful AI technology
- Patent DNA Extraction
Browse by: Latest US Patents, China's latest patents, Technical Efficacy Thesaurus, Application Domain, Technology Topic, Popular Technical Reports.
© 2024 PatSnap. All rights reserved.Legal|Privacy policy|Modern Slavery Act Transparency Statement|Sitemap|About US| Contact US: help@patsnap.com