Modified high-nickel positive electrode material and preparation method thereof
A positive electrode material and high-nickel technology, applied in chemical instruments and methods, battery electrodes, nickel compounds, etc., can solve the problems of reducing the discharge capacity and cycle life of materials, increasing the difficulty of pulping and coating, and serious battery gas production. Achieve the effects of improving structural stability and cycle stability, alleviating gas production, and reducing the amount of residual alkali on the surface
- Summary
- Abstract
- Description
- Claims
- Application Information
AI Technical Summary
Problems solved by technology
Method used
Image
Examples
preparation example Construction
[0032] A preparation method for surface modification of a high-nickel positive electrode material, comprising the following steps:
[0033] Step 1: Raw material preparation: Mix the precursor of high-nickel positive electrode material, additives and lithium source evenly, place it in high-temperature equipment for primary sintering under an oxygen atmosphere, and obtain a primary sintered high-nickel positive electrode material after crushing and sieving the material;
[0034] Step 2: mixing and stirring the primary sintered high-nickel positive electrode material with deionized water, separating the solid from the liquid, and drying the solid to obtain the primary sintered high-nickel positive electrode material after washing and drying;
[0035] Step 3: Place the primary sintered high-nickel positive electrode material after washing and drying in a high-temperature device to perform a surface treatment to obtain a surface-treated high-nickel positive electrode material;
[0...
Embodiment 1
[0056] Step 1. Mix lithium hydroxide, nickel-cobalt-aluminum hydroxide and additive magnesium hydroxide uniformly to obtain a mixture, wherein the molar ratio of the three metal elements of nickel-cobalt-aluminum in the nickel-cobalt-aluminum hydroxide precursor is 91:6: 3, that is, x is 0.06, y is 0.03, the ratio of the amount of lithium hydroxide to the precursor of nickel-cobalt-aluminum hydroxide is 0.9:1, that is, n is 0.9, and the content of magnesium in magnesium hydroxide is nickel-cobalt-aluminum 0.5% of the amount of hydroxide species, ie z is 0.05.
[0057] The mixture is placed in high-temperature equipment and calcined under an oxygen atmosphere. The calcining is carried out in two stages. The first stage calcining temperature is 420°C and the holding time is 10h. The second stage calcining temperature is 650°C and the holding time is 16h. Then Cooling, crushing, and sieving through a 300-mesh sieve to obtain a primary sintered nickel-cobalt-lithium aluminate tern...
Embodiment 1 and comparative example 1
[0064] Embodiment 1 and comparative example 1 performance detection
[0065] Using the lithium cobalt aluminate with low lithium ratio in Example 1 of the present invention and the lithium cobalt aluminate with high lithium ratio in Comparative Example 1, respectively take 5g of powder samples and place them in 95g of deionized aqueous solution, stir for 5min and then suction filter. Use the Mettler toledo T50 potentiometric titrator to measure Li in the solution in the material according to the equivalence point 2 CO 3 and the content of LiOH, and take the content as the residual alkali content on the surface of the material. It can be seen from Table 1 that the nickel-cobalt-aluminum anode material prepared with a lower lithium ratio in Example 1 of the present invention has significantly lower residual alkali on the surface of the material.
PUM
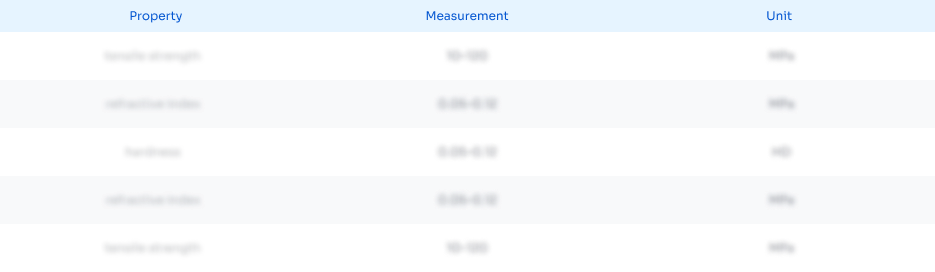
Abstract
Description
Claims
Application Information

- R&D Engineer
- R&D Manager
- IP Professional
- Industry Leading Data Capabilities
- Powerful AI technology
- Patent DNA Extraction
Browse by: Latest US Patents, China's latest patents, Technical Efficacy Thesaurus, Application Domain, Technology Topic, Popular Technical Reports.
© 2024 PatSnap. All rights reserved.Legal|Privacy policy|Modern Slavery Act Transparency Statement|Sitemap|About US| Contact US: help@patsnap.com