Cigarette cooling composite film and application thereof
A composite film and cigarette technology, applied in the field of cigarettes, to achieve the effects of easy availability of raw materials, improved heat absorption capacity, and simple preparation process
- Summary
- Abstract
- Description
- Claims
- Application Information
AI Technical Summary
Problems solved by technology
Method used
Image
Examples
Embodiment 1
[0032] Weigh 20g of polyethylene glycol 4000 and 30g of polyacrylic acid and disperse them in 50g of water, ultrasonicate for 3 hours to form a uniform system, cast into a film, volatilize the solvent (water) and dry to obtain a cooling composite film. figure 1 Be the scanning electron microscope picture (SEM) of the cross-section of the cooling composite thin film of the present embodiment, figure 2 Be the SEM figure of the cooling composite film surface of the present embodiment, by figure 1 and figure 2 It can be seen that the phase change component (polyethylene glycol) has been uniformly immobilized in the cooling composite film substrate. The cooling composite film is rolled into a sheet with wrinkles, and the sheet is made into a cooling filter rod through a paper nozzle rod forming process, and the cooling filter rod is cut into cooling sections with a length of 15 mm. The cooling section is placed between the tobacco section and the cellulose acetate filter sectio...
Embodiment 2
[0034] Weigh 20g of palmitic alcohol and 10g of polyethylene oxide and disperse them in 100g of water / ethanol binary solution (the mass ratio of water to ethanol is 1:1), stir mechanically at a stirring speed of 1000 rpm for 6 hours to form a uniform system, and cast Form a film, volatilize the solvent (water and ethanol) and dry to obtain a cooling composite film. image 3 Be the SEM figure of the cooling composite film surface of the present embodiment, by image 3 It can be seen that the phase change material (palmityl alcohol) has been uniformly immobilized in the cooling composite film substrate. The cooling composite film is rolled into a sheet with wrinkles, and the sheet is made into a cooling filter rod through a paper nozzle rod forming process, and the cooling filter rod is cut into cooling sections with a length of 15 mm. The cooling section is placed between the tobacco section and the cellulose acetate filter section of the heat-not-burn cigarette to obtain a ci...
Embodiment 3
[0036] The mixed solution that takes by weighing 10g stearic acid and certain volume is formed by 5g formaldehyde, 8g phenol, 1g sodium hydroxide, 1.2g resorcinol, 0.13g petroleum sodium sulfonate is dispersed in 50g water / ethanol binary solution ( The mass ratio of water to ethanol is 4:1), and the volume ratio of the mixed solution to the water / ethanol binary solution is 2:1. After ultrasonically forming a stable emulsion, it is heated to 75°C for 4 hours, cooled to room temperature, and then cast into a film, the solvents (water and ethanol) were evaporated and dried to obtain a cooling composite film. The cooling composite film is rolled into a sheet with wrinkles, and the sheet is made into a cooling filter rod through a paper nozzle rod forming process, and the cooling filter rod is cut into cooling sections with a length of 15 mm. The cooling section is placed between the tobacco section and the cellulose acetate filter section of the heat-not-burn cigarette to obtain a...
PUM
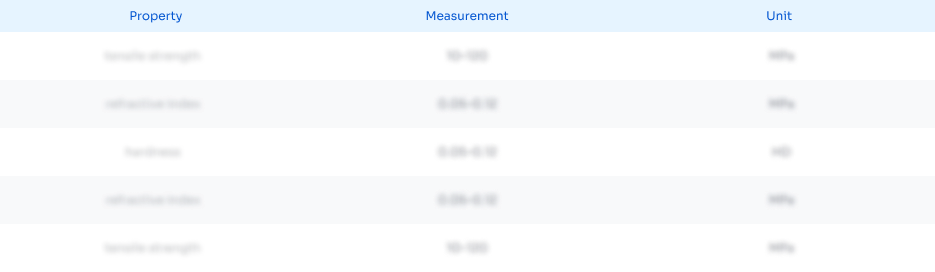
Abstract
Description
Claims
Application Information

- Generate Ideas
- Intellectual Property
- Life Sciences
- Materials
- Tech Scout
- Unparalleled Data Quality
- Higher Quality Content
- 60% Fewer Hallucinations
Browse by: Latest US Patents, China's latest patents, Technical Efficacy Thesaurus, Application Domain, Technology Topic, Popular Technical Reports.
© 2025 PatSnap. All rights reserved.Legal|Privacy policy|Modern Slavery Act Transparency Statement|Sitemap|About US| Contact US: help@patsnap.com