Flame-retardant master batch and preparation method thereof
A technology of flame retardant masterbatch and flame retardant synergist, used in the field of flame retardant materials, can solve the problems of small molecular weight, low heat resistance, high volatility, etc., to speed up the rupture, shorten the contact time, and improve the resistance. burning effect
- Summary
- Abstract
- Description
- Claims
- Application Information
AI Technical Summary
Problems solved by technology
Method used
Examples
Embodiment 1
[0047] Embodiment 1: a kind of preparation method of flame retardant masterbatch, comprises the following steps:
[0048] S1, preparation of microcapsule flame retardant synergist;
[0049] S11. Weigh β-cyclodextrin and antimony trioxide, wherein the weight-number ratio of antimony trioxide and β-cyclodextrin is 1:4;
[0050] S12. Dissolving β-cyclodextrin in water and stirring evenly to form an embedding solution, wherein the weight-number ratio of β-cyclodextrin to water is 1:5;
[0051] S13. Add antimony trioxide into the embedding solution, and stir evenly under the conditions of 33° C. and 10,000 r / min to obtain a microcapsule flame retardant synergist solution;
[0052] S14. The microcapsule flame retardant synergist solution is sprayed and condensed to granulate through a centrifugal spray tower to prepare the microcapsule flame retardant synergist;
[0053] S2, drying 100 parts of polypropylene at 80° C. for 3 hours to obtain dried polypropylene;
[0054] S3, mix 0....
Embodiment 2
[0056] Embodiment 2: a kind of preparation method of flame retardant masterbatch, comprises the following steps:
[0057] S1, preparation of microcapsule flame retardant synergist;
[0058] S11. Weigh β-cyclodextrin and antimony trioxide, wherein the weight-number ratio of antimony trioxide and β-cyclodextrin is 1:5;
[0059] S12. Dissolving β-cyclodextrin in water and stirring evenly to form an embedding solution, wherein the weight-number ratio of β-cyclodextrin to water is 1:6;
[0060] S13. Add antimony trioxide into the embedding solution, and stir evenly under the conditions of 33° C. and 10,000 r / min to obtain a microcapsule flame retardant synergist solution;
[0061] S14. The microcapsule flame retardant synergist solution is sprayed and condensed to granulate through a centrifugal spray tower to prepare the microcapsule flame retardant synergist;
[0062] S2. Drying 110 parts of polypropylene at 80° C. for 3 hours to obtain dried polypropylene;
[0063] S3, 1.5 pa...
Embodiment 3
[0065] Embodiment 3: a kind of preparation method of flame retardant masterbatch, comprises the following steps:
[0066] S1, preparation of microcapsule flame retardant synergist;
[0067] S11. Weigh β-cyclodextrin and antimony trioxide, wherein the weight-number ratio of antimony trioxide and β-cyclodextrin is 1:6;
[0068] S12. Dissolving β-cyclodextrin in water and stirring evenly to form an embedding solution, wherein the weight-number ratio of β-cyclodextrin to water is 1:7;
[0069] S13. Add antimony trioxide into the embedding solution, and stir evenly under the conditions of 33° C. and 10,000 r / min to obtain a microcapsule flame retardant synergist solution;
[0070] S14. The microcapsule flame retardant synergist solution is sprayed and condensed to granulate through a centrifugal spray tower to prepare the microcapsule flame retardant synergist;
[0071] S2, drying 120 parts of polypropylene at 80° C. for 3 hours to obtain dried polypropylene;
[0072] S3, 3 part...
PUM
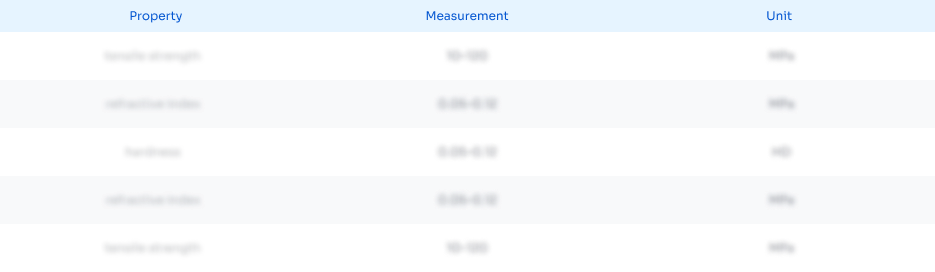
Abstract
Description
Claims
Application Information

- R&D
- Intellectual Property
- Life Sciences
- Materials
- Tech Scout
- Unparalleled Data Quality
- Higher Quality Content
- 60% Fewer Hallucinations
Browse by: Latest US Patents, China's latest patents, Technical Efficacy Thesaurus, Application Domain, Technology Topic, Popular Technical Reports.
© 2025 PatSnap. All rights reserved.Legal|Privacy policy|Modern Slavery Act Transparency Statement|Sitemap|About US| Contact US: help@patsnap.com