Robot joint part with cooling structure, power joint and robot
A technology of robot joints and heat dissipation structure, which is applied in the field of robots, can solve the problems of excessive external liquid cooling auxiliary devices, large output loads of robot power joints, compact structure size, and low heat dissipation efficiency, so as to speed up speed and heat exchange efficiency, eliminate Heat accumulation, good cooling effect
- Summary
- Abstract
- Description
- Claims
- Application Information
AI Technical Summary
Problems solved by technology
Method used
Image
Examples
Embodiment Construction
[0035] In order to make the purpose, technical solutions and advantages of the embodiments of the present invention more clear, the embodiments of the present invention will be further described in detail below in conjunction with the accompanying drawings. Here, the exemplary embodiments and descriptions of the present invention are used to explain the present invention, but not to limit the present invention. In the drawings of the present invention, the same reference numerals represent the same or similar components.
[0036] Here, it should be noted that, in order to avoid obscuring the present invention due to unnecessary details, only the structures and / or processing steps that are closely related to the solution according to the present invention are shown in the drawings, while those related to the present invention are omitted. Invent other details that don't really matter.
[0037] It should be emphasized that the term "comprises / comprises / has" when used herein ref...
PUM
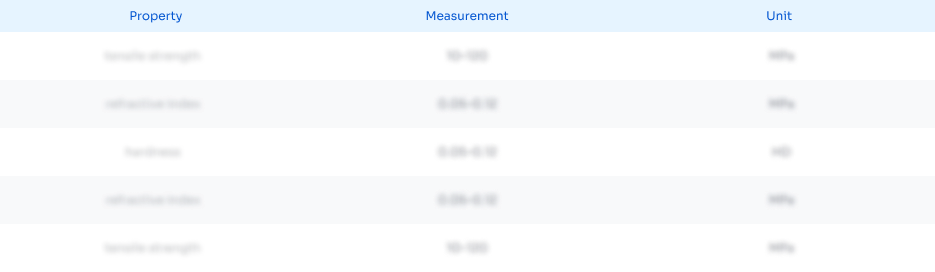
Abstract
Description
Claims
Application Information

- R&D
- Intellectual Property
- Life Sciences
- Materials
- Tech Scout
- Unparalleled Data Quality
- Higher Quality Content
- 60% Fewer Hallucinations
Browse by: Latest US Patents, China's latest patents, Technical Efficacy Thesaurus, Application Domain, Technology Topic, Popular Technical Reports.
© 2025 PatSnap. All rights reserved.Legal|Privacy policy|Modern Slavery Act Transparency Statement|Sitemap|About US| Contact US: help@patsnap.com