Modified graphene oxide epoxy resin composite coating and preparation method thereof
A technology of ethylene epoxy resin and composite coating, which is applied in the direction of epoxy resin coating, anti-corrosion coating, coating, etc., can solve the problems of insufficient anti-corrosion coating technology and performance, and achieve the effect of compact structure and good anti-corrosion performance
- Summary
- Abstract
- Description
- Claims
- Application Information
AI Technical Summary
Problems solved by technology
Method used
Examples
Embodiment 1
[0026] (1) Add 10 g of sodium bicarbonate (NaHCO 3 ) and 186.6 mg disodium ethylenediaminetetraacetate (EDTA.2Na), stirred evenly to form a dialysate, placed the dialysis bag in the dialysate and boiled for 15 min, then washed the dialysis bag with distilled water several times, and then washed the dialysate Put the bag in 1 mmol / L EDTA.2Na solution (PH=8.0) and boil for 10 min;
[0027] (2) Dissolve an appropriate amount of graphite oxide slurry in distilled water, sonicate for 30 min, then put it into a cooled dialysis bag and magnetically stir it in a beaker filled with distilled water for 3 d. Finally, ultrasonic peeling was carried out for a total of 3 times at 0°C for 30 minutes by an ultrasonic cell disruptor to obtain a graphene oxide dispersion;
[0028] (3) Weigh 10 ml of graphene oxide dispersion and place it in a beaker, add 160 ml of distilled water, put it in an oven to dry for 5 hours, and measure its solid content to be 9 mg / ml;
[0029] (4) Measure 8.9ml of...
Embodiment 2
[0036] (1) Add 10 g of sodium bicarbonate (NaHCO 3 ) and 186.6 mg of ethylenediaminetetraacetic acid disodium (EDTA.2Na), stirred evenly to prepare a dialysate, placed the dialysis bag in the dialysate and boiled for 15 min, then washed the dialysis bag with distilled water several times, and then washed the dialysate Put the bag in 1 mmol / L EDTA.2Na solution (PH=8.0) and boil for 10 min;
[0037] (2) Dissolve an appropriate amount of graphite oxide slurry in distilled water, sonicate for 40 min, then put it into a cooled dialysis bag and stir magnetically for 3 days in a beaker filled with distilled water. Finally, ultrasonic peeling was carried out for 40 minutes under the condition of 5°C by an ultrasonic cell disruptor for a total of 4 times to obtain a dispersion of graphene oxide;
[0038] (3) Weigh 10ml of the graphene oxide dispersion and place it in a beaker, add 160ml of distilled water, put it in an oven and dry it for 5 hours, and measure its solid content to be ...
Embodiment 3
[0046] (1) Add 10 g of sodium bicarbonate (NaHCO 3 ) and 186.6 mg disodium ethylenediaminetetraacetate (EDTA.2Na), stirred evenly to form a dialysate, placed the dialysis bag in the dialysate and boiled for 15 min, then washed the dialysis bag with distilled water several times, and then washed the dialysate Put the bag in 1 mmol / L EDTA.2Na solution (PH=8.0) and boil for 10 min;
[0047] (2) Dissolve an appropriate amount of graphite oxide slurry in distilled water, sonicate for 30 min, then put it into a cooled dialysis bag and magnetically stir it in a beaker filled with distilled water for 4 d. Finally, ultrasonic peeling was carried out for a total of 4 times at 3°C for 40 minutes by an ultrasonic cell disruptor to obtain a graphene oxide dispersion;
[0048] (3) Weigh 10ml of the graphene oxide dispersion and place it in a beaker, add 160ml of distilled water, put it in an oven and dry it for 5 hours, and measure its solid content to be 9mg / ml;
[0049] (4) Measure 8...
PUM
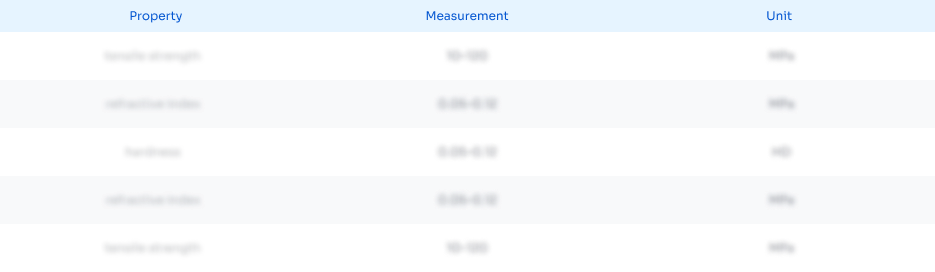
Abstract
Description
Claims
Application Information

- Generate Ideas
- Intellectual Property
- Life Sciences
- Materials
- Tech Scout
- Unparalleled Data Quality
- Higher Quality Content
- 60% Fewer Hallucinations
Browse by: Latest US Patents, China's latest patents, Technical Efficacy Thesaurus, Application Domain, Technology Topic, Popular Technical Reports.
© 2025 PatSnap. All rights reserved.Legal|Privacy policy|Modern Slavery Act Transparency Statement|Sitemap|About US| Contact US: help@patsnap.com