Ultra-low emission method and device for sulfur recovery tail gas
A sulfur recovery tail gas and sulfur recovery technology, applied in separation methods, chemical instruments and methods, gas treatment, etc., can solve the problems of high cost, complicated process, secondary pollution, etc., and achieve extended life, simple equipment, and reduced corrosion Effect
- Summary
- Abstract
- Description
- Claims
- Application Information
AI Technical Summary
Problems solved by technology
Method used
Image
Examples
Embodiment 1
[0020] Embodiment 1: as attached figure 1 As shown, the method for the ultra-low emission of the sulfur recovery tail gas is carried out according to the following steps: the first step, the high temperature sulfur recovery mixed tail gas enters the WSA condenser 1 through the sulfuric acid process gas pipeline 9, and enters through the cold air pipeline 8 The cold air in the WSA condenser 1 undergoes heat exchange and cools down to become a low-temperature sulfur recovery mixed tail gas, and the temperature of the cold air rises to become hot air; in the second step, the low-temperature sulfur recovery mixed tail gas is discharged from the upper outlet of the WSA condenser 1, and is discharged from the first A sulfur recovery tail gas treatment pipeline 10 enters the acid mist trap 2, and the low-temperature acid mist entrained in the low-temperature sulfur recovery tail gas is further captured by the acid mist trap 2. After the hot air is discharged through the lower gas outl...
Embodiment 2
[0022] Embodiment 2: As an optimization of the above embodiment, in the low-temperature sulfur recovery mixed tail gas, the temperature of the sulfur recovery mixed tail gas is 80°C to 104°C. The sulfur content in the acid mist entrained by the low-temperature sulfur recovery mixed tail gas after the heat exchange of WSA condenser 1 can be reduced to 50mg / Nm 3 .
[0023] The high-temperature sulfuric acid-containing process gas (high-temperature sulfur recovery tail gas) fed into the condenser 1 conducts heat exchange and cooling with the cold air, which can not only enable the acid mist collector 2 to better capture the acid mist, but also make rational use of the hot air. Control the mixing ratio of the hot air and the sulfur recovery tail gas captured by the acid mist collector 2 to 2:1, so that the temperature of the sulfur recovery tail gas in the mixer 4 is 130°C to 160°C, effectively reducing the acid mist in the tail gas Condensation in the third sulfur recovery tail ...
Embodiment 3
[0024] Embodiment 3: As an optimization of the above embodiment, the sulfuric acid recovery pipeline is an inverted U-shaped pipeline. The inverted U-shaped recovery sulfuric acid pipeline can make the liquid in the pipeline quickly return to the acid intermediate storage tank 3 by utilizing the high head difference.
PUM
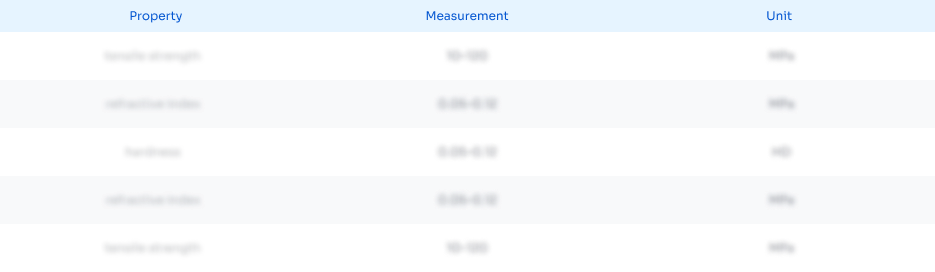
Abstract
Description
Claims
Application Information

- Generate Ideas
- Intellectual Property
- Life Sciences
- Materials
- Tech Scout
- Unparalleled Data Quality
- Higher Quality Content
- 60% Fewer Hallucinations
Browse by: Latest US Patents, China's latest patents, Technical Efficacy Thesaurus, Application Domain, Technology Topic, Popular Technical Reports.
© 2025 PatSnap. All rights reserved.Legal|Privacy policy|Modern Slavery Act Transparency Statement|Sitemap|About US| Contact US: help@patsnap.com