Recovery process of valuable components in waste thick film
A process and thick film technology, applied in the field of recycling valuable metals, can solve the problems of waste of resources, high energy consumption, high risk of recycling operations, and achieve the effect of less exhaust gas emissions and simple process flow
- Summary
- Abstract
- Description
- Claims
- Application Information
AI Technical Summary
Problems solved by technology
Method used
Examples
Embodiment 1
[0035] The waste thick film circuit is disassembled from the product by mechanical dismantling, and then the disassembled thick film is leached in the mixed acid solution of nitric acid and sulfuric acid according to the solid-liquid ratio of 1:5 (the nitric acid The volume ratio of sulfuric acid to sulfuric acid is 9:1), and the leaching process is stirred and leached for 5 hours at a reaction temperature of 65°C to separate the thick-film ceramics from the stainless steel; the thick-film ceramic components are dried and ground with a ball mill to obtain ceramic powder, and then The ceramic powder is subjected to hydraulic gravity separation with a gravity separator to obtain a powder containing ruthenium dioxide, and finally the powder containing ruthenium dioxide is treated with hydrofluoric acid and recovered, and the recovery rate of ruthenium dioxide is about 90%.
Embodiment 2
[0037] The waste thick film circuit is disassembled from the product by mechanical disassembly, and then the disassembled thick film is leached in nitric acid according to the ratio of solid to liquid ratio of 1:3. The leaching process is carried out at a reaction temperature of 70°C. Stir and leach for 5 hours to separate the thick-film ceramics from the stainless steel; after drying, the ceramic components are ground with a ball mill to obtain ceramic powder, and then the ceramic powder is subjected to hydraulic gravity separation with a gravity separator to obtain a gold-containing powder. Finally, the gold-containing powder is recovered after treatment with hydrofluoric acid, and the recovery rate of gold is about 83%.
Embodiment 3
[0039] The waste thick film circuit is disassembled from the product by mechanical dismantling, and then the disassembled thick film is leached in the mixed acid solution of nitric acid and sulfuric acid according to the solid-liquid ratio of 1:9 (the nitric acid The volume ratio of sulfuric acid to sulfuric acid is 10:1), and the leaching process is stirred and leached for 15 hours at a reaction temperature of 45°C to separate the thick-film ceramics from the stainless steel; the thick-film ceramic components are dried and ground with a ball mill to obtain ceramic powder, and then The ceramic powder is separated by hydraulic gravity with a gravity separator to obtain platinum-containing powder. Finally, the platinum-containing powder is treated with hydrofluoric acid and recovered. The recovery rate of platinum is about 81%.
PUM
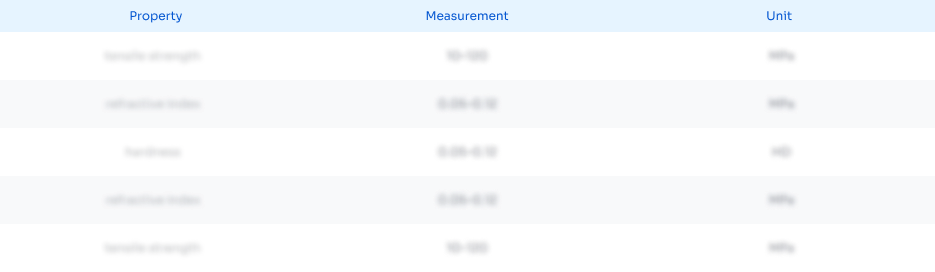
Abstract
Description
Claims
Application Information

- R&D
- Intellectual Property
- Life Sciences
- Materials
- Tech Scout
- Unparalleled Data Quality
- Higher Quality Content
- 60% Fewer Hallucinations
Browse by: Latest US Patents, China's latest patents, Technical Efficacy Thesaurus, Application Domain, Technology Topic, Popular Technical Reports.
© 2025 PatSnap. All rights reserved.Legal|Privacy policy|Modern Slavery Act Transparency Statement|Sitemap|About US| Contact US: help@patsnap.com