Autogenous grinding type roller replacement reactor and re-dissolution-resisting multi-energy cascade purge technology
A reactor and self-grinding technology, which is applied in the direction of photography technology, photography auxiliary technology, and process efficiency improvement, can solve the problems of large land occupation, large consumption of zinc powder, and many processing equipment.
- Summary
- Abstract
- Description
- Claims
- Application Information
AI Technical Summary
Problems solved by technology
Method used
Image
Examples
Embodiment 1
[0038] like Figure 1-6 The self-grinding drum displacement reactor shown includes a displacement reactor 1, a liquid inlet 2, a liquid outlet 3, a supporting ring 4, a supporting wheel 5, a ring gear 6, a driving device 7, a driving ring gear 8, Enhanced self-grinding tank 9, feeding hole 10, lifting plate 11, and powder lifting plate 12, characterized in that: the displacement reactor 1 is designed as a drum, and one end of the displacement reactor 1 is provided with a liquid inlet 2, and the displacement reactor 1 The other end of the displacement reactor 1 is provided with a liquid outlet 3, and the two ends of the outer surface of the cylinder of the displacement reactor 1 are respectively provided with support rings 4, and the two support rings 4 are placed on two sets of supporting wheels 5 oppositely arranged at the bottom of the displacement reactor 1. The outer surface of the cylinder of the displacement reactor 1 between the supporting rings 4 is provided with a rin...
PUM
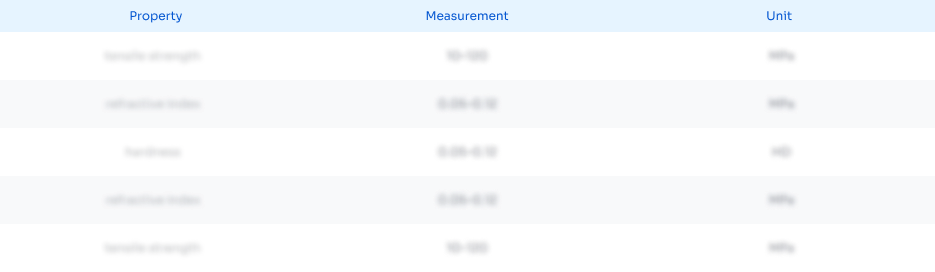
Abstract
Description
Claims
Application Information

- R&D
- Intellectual Property
- Life Sciences
- Materials
- Tech Scout
- Unparalleled Data Quality
- Higher Quality Content
- 60% Fewer Hallucinations
Browse by: Latest US Patents, China's latest patents, Technical Efficacy Thesaurus, Application Domain, Technology Topic, Popular Technical Reports.
© 2025 PatSnap. All rights reserved.Legal|Privacy policy|Modern Slavery Act Transparency Statement|Sitemap|About US| Contact US: help@patsnap.com