Epoxy resin suitable for pultrusion process and carbon fiber composite material thereof
An epoxy resin and pultrusion molding technology, which is applied in the field of carbon fiber, can solve the problems of high chemical activity of amine curing agent, affecting the molding process of the pulling agent, and affecting the performance of the resin system, so as to achieve the mechanical properties and heat resistance of the cured product Excellent, long pot life, the effect of improving production efficiency
- Summary
- Abstract
- Description
- Claims
- Application Information
AI Technical Summary
Problems solved by technology
Method used
Image
Examples
Embodiment 1
[0023] A low-viscosity epoxy resin system suitable for the drawing agent molding process of this embodiment is a two-component system, the A component is a compounded epoxy resin, and the B component is a curing agent. According to parts by weight, A:B=100:80~110;
[0024] Component A of the resin system includes: 1. Main resin: one or more of bisphenol A type epoxy resin, bisphenol F type resin, and novolac epoxy resin, calculated by weight percentage, the proportion of A component is 50% to 80%; 2. Toughening agent: one or more of nuclear rubber modified epoxy resin, polyurethane modified epoxy resin, and polyethersulfone modified epoxy resin, calculated by weight percentage, accounting for A The proportion of components is 5% to 30%; 3. Diluent: one or two kinds of active diluent and inactive diluent, calculated according to weight percentage, accounting for 30% to 10% of component A;
[0025] The B component of the resin system includes: the curing agent is an acid anhydr...
Embodiment 2
[0041] A carbon fiber composite material using a stretching agent forming process in this embodiment;
[0042] Inject the above compounded components A and B into the injection machine respectively, mix them evenly and inject them into the curing mold, and at the same time introduce the fiber and release cloth into the curing mold for curing and molding. The fibers are carbon fibers or glass fibers.
[0043] One of the low-viscosity liquid resins prepared above and the continuous carbon fiber (T300) were used to prepare a carbon fiber composite material through a stretching agent molding process, and the mechanical properties were tested as shown in Table 2;
PUM
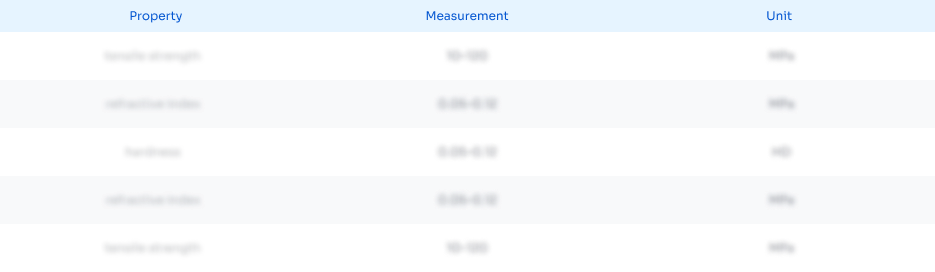
Abstract
Description
Claims
Application Information

- R&D Engineer
- R&D Manager
- IP Professional
- Industry Leading Data Capabilities
- Powerful AI technology
- Patent DNA Extraction
Browse by: Latest US Patents, China's latest patents, Technical Efficacy Thesaurus, Application Domain, Technology Topic, Popular Technical Reports.
© 2024 PatSnap. All rights reserved.Legal|Privacy policy|Modern Slavery Act Transparency Statement|Sitemap|About US| Contact US: help@patsnap.com