Injection molding mechanism for fast blanking and operation method thereof
A rapid and injection molding technology, applied in the field of mold forming, can solve problems that affect product quality, increase production costs, and safety hazards
- Summary
- Abstract
- Description
- Claims
- Application Information
AI Technical Summary
Problems solved by technology
Method used
Image
Examples
Embodiment Construction
[0033] The technical solutions of the present invention will be clearly and completely described below in conjunction with the embodiments. Apparently, the described embodiments are only some of the embodiments of the present invention, not all of them. Based on the embodiments of the present invention, all other embodiments obtained by persons of ordinary skill in the art without creative efforts fall within the protection scope of the present invention.
[0034] see Figure 1-9 As shown, a rapid blanking injection molding mechanism includes a feeding box 1, an injection molding box 4 and an injection molding device 5, the feeding box 1 is installed on the top side of the base 6, and the injection molding box 4 is installed on the top of the base 6 On the other side of the surface, a feeding funnel 2 is arranged on the top surface of the feeding box 1, and an injection molding device 5 is arranged in the injection molding box 4. The feeding end on one side of the injection mo...
PUM
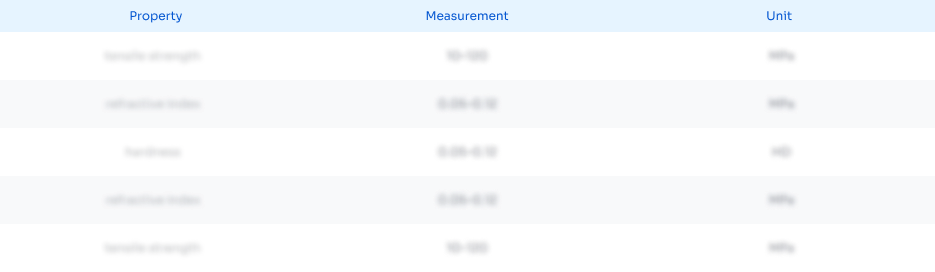
Abstract
Description
Claims
Application Information

- Generate Ideas
- Intellectual Property
- Life Sciences
- Materials
- Tech Scout
- Unparalleled Data Quality
- Higher Quality Content
- 60% Fewer Hallucinations
Browse by: Latest US Patents, China's latest patents, Technical Efficacy Thesaurus, Application Domain, Technology Topic, Popular Technical Reports.
© 2025 PatSnap. All rights reserved.Legal|Privacy policy|Modern Slavery Act Transparency Statement|Sitemap|About US| Contact US: help@patsnap.com