Preparation method of fluorine-containing polymer powder
A polymer and powder technology, which is applied in the field of preparation of fluorine-containing polymer powder, can solve the problems of high energy consumption and achieve the effects of reducing the amount of coagulation agent, saving production costs and shortening the coagulation time
- Summary
- Abstract
- Description
- Claims
- Application Information
AI Technical Summary
Problems solved by technology
Method used
Examples
Embodiment 1
[0034] Press 70L of ethylene-chlorotrifluoroethylene (ECTFE) emulsion with a solid content of 11.2% into the coagulation bucket, add 280L of deionized water to dilute, and the diluted emulsion has a solid content of 2.2%. Turn on the stirring, stir the ECTFE emulsion in the coagulation barrel at 250rpm, and raise the temperature of the ECTFE emulsion to 55°C while stirring. Add 150 g of calcium chloride into the coagulation bucket, increase the stirring speed to 2000 rpm, and continue stirring for 20 minutes. Obtain the ECTFE resin that demulsification separates out after stopping stirring. Wash the ECTFE resin separated by demulsification with normal temperature deionized water until the conductivity is less than 5 μS / cm, and dry it in an oven at 105° C. for 24 hours to obtain ECTFE powder.
[0035] After demulsification and precipitation of ECTFE resin, the coagulation wastewater is clear and transparent, with a solid content of 0.12% and a coagulation efficiency of 99.88%....
Embodiment 2
[0037] Press 80L of ECTFE emulsion with a solid content of 15.1% into the coagulation bucket, add 320L of deionized water to dilute, and the diluted emulsion has a solid content of 3.0%. Turn on the stirring, stir the ECTFE emulsion in the coagulation bucket at 280rpm, and raise the temperature of the ECTFE emulsion to 60°C while stirring. Add 200 g of calcium chloride to the coagulation barrel, increase the stirring speed to 2200 rpm, and continue stirring for 20 minutes. Obtain the ECTFE resin that demulsification separates out after stopping stirring. Wash the ECTFE resin separated by demulsification with normal temperature deionized water until the conductivity is less than 5 μS / cm, and dry it in an oven at 105° C. for 24 hours to obtain ECTFE powder.
[0038] After demulsification and precipitation of ECTFE resin, the coagulation wastewater is clear and transparent, with a solid content of 0.11% and a coagulation efficiency of 99.89%.
Embodiment 3
[0040] Press 60L of ECTFE emulsion with a solid content of 19.7% into the coagulation barrel, add 412L of deionized water to dilute, and the diluted emulsion has a solid content of 2.5%. Turn on the stirring, stir the ECTFE emulsion in the coagulation bucket at 300rpm, and raise the temperature of the ECTFE emulsion to 60°C while stirring. Add 180 g of calcium chloride into the coagulation bucket, increase the stirring speed to 2300 rpm, and continue stirring for 25 minutes. Obtain the ECTFE resin that demulsification separates out after stopping stirring. Wash the ECTFE resin separated by demulsification with normal temperature deionized water until the conductivity is less than 5 μS / cm, and dry it in an oven at 105° C. for 24 hours to obtain ECTFE powder.
[0041]After demulsification and precipitation of ECTFE resin, the coagulation wastewater is clear and transparent, with a solid content of 0.09% and a coagulation efficiency of 99.91%.
PUM
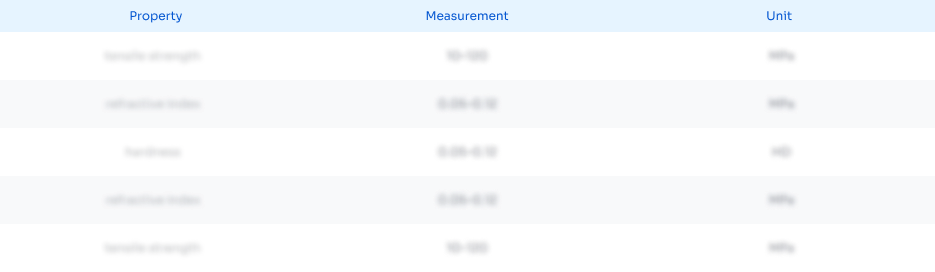
Abstract
Description
Claims
Application Information

- R&D
- Intellectual Property
- Life Sciences
- Materials
- Tech Scout
- Unparalleled Data Quality
- Higher Quality Content
- 60% Fewer Hallucinations
Browse by: Latest US Patents, China's latest patents, Technical Efficacy Thesaurus, Application Domain, Technology Topic, Popular Technical Reports.
© 2025 PatSnap. All rights reserved.Legal|Privacy policy|Modern Slavery Act Transparency Statement|Sitemap|About US| Contact US: help@patsnap.com