Preparation method of vinyl phenyl silicone oil with high phenyl content
A vinyl phenyl silicon, high phenyl technology, applied in the field of preparation of vinyl phenyl silicone oil, can solve the problems of low refractive index and light transmittance of phenyl silicone oil, and achieve high phenyl content and good light transmittance , the effect of high refractive index
- Summary
- Abstract
- Description
- Claims
- Application Information
AI Technical Summary
Problems solved by technology
Method used
Examples
Embodiment 1
[0020] Follow the steps below to prepare vinylphenyl silicone oil with high phenyl content:
[0021] (1) DMC and tetramethylammonium hydroxide pentahydrate with a mass ratio of 70:30 are heated to 75° C., stirred and mixed for 5 hours at a speed of 400 r / min, and vacuumized to reflux to remove water to obtain an alkali gel catalyst;
[0022] (2) Heat octamethylcyclotetrasiloxane and octaphenylcyclotetrasiloxane with a mass ratio of 75:25 to 75°C, stir and mix for 75 minutes, and vacuum dehydrate for 1 hour to obtain methylphenylcyclotetrasiloxane oxane mixture;
[0023] (3) Add divinyltetraphenyldisiloxane to the methylphenylcyclosiloxane mixture obtained in step (2) and mix evenly, then add the alkali gel catalyst obtained in step (1) and heat it to 100°C for 400r Stirring and mixing at a speed of 1 / min for 5 hours obtained the mixture, and the mass ratio of divinyltetraphenyldisiloxane, methylphenylcyclosiloxane mixture and alkali gel catalyst was 2:100:1;
[0024] (4) Con...
Embodiment 2
[0026] Follow the steps below to prepare vinylphenyl silicone oil with high phenyl content:
[0027] (1) DMC and tetramethylammonium hydroxide pentahydrate with a mass ratio of 60:20 are heated to 70° C., stirred and mixed for 4 hours at a speed of 600 r / min, and vacuumized to reflux to remove water to obtain an alkali gel catalyst;
[0028] (2) Heat octamethylcyclotetrasiloxane and octaphenylcyclotetrasiloxane with a mass ratio of 65:15 to 70°C, stir and mix for 90 minutes, and vacuum dehydrate for 1 hour to obtain methylphenylcyclotetrasiloxane oxane mixture;
[0029] (3) Add divinyltetraphenyldisiloxane to the methylphenylcyclosiloxane mixture obtained in step (2) and mix evenly, then add the alkali gel catalyst obtained in step (1), heat to 90°C and then 600r Stirring and mixing at a speed of 1 / min for 4 hours to obtain the mixture, the mass ratio of divinyltetraphenyldisiloxane, methylphenylcyclosiloxane mixture, alkali gel catalyst is 1:100:1;
[0030] (4) Continue to ...
Embodiment 3
[0032] Follow the steps below to prepare vinylphenyl silicone oil with high phenyl content:
[0033] (1) DMC and tetramethylammonium hydroxide pentahydrate having a mass ratio of 80:40 are heated up to 80° C., stirred and mixed for 6 hours at a speed of 300 r / min, and vacuumized to reflux to remove water to obtain an alkali gel catalyst;
[0034] (2) Heat octamethylcyclotetrasiloxane and octaphenylcyclotetrasiloxane with a mass ratio of 85:30 to 80°C, stir and mix for 60 minutes, and vacuum dehydrate for 1 hour to obtain methylphenylcyclotetrasiloxane oxane mixture;
[0035] (3) Add divinyltetraphenyldisiloxane to the methylphenylcyclosiloxane mixture obtained in step (2) and mix evenly, then add the alkali gel catalyst obtained in step (1), heat to 110°C and then 300r Stirring and mixing at a speed of 1 / min obtained the mixture for 6 hours, and the mass ratio of divinyltetraphenyldisiloxane, methylphenylcyclosiloxane mixture and alkali gel catalyst was 3:100:1;
[0036] (4)...
PUM
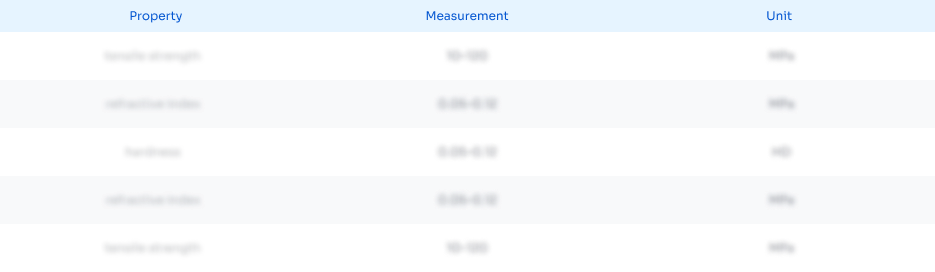
Abstract
Description
Claims
Application Information

- Generate Ideas
- Intellectual Property
- Life Sciences
- Materials
- Tech Scout
- Unparalleled Data Quality
- Higher Quality Content
- 60% Fewer Hallucinations
Browse by: Latest US Patents, China's latest patents, Technical Efficacy Thesaurus, Application Domain, Technology Topic, Popular Technical Reports.
© 2025 PatSnap. All rights reserved.Legal|Privacy policy|Modern Slavery Act Transparency Statement|Sitemap|About US| Contact US: help@patsnap.com