Resin protective film material and preparation method thereof
A protective film and resin technology, applied in the field of new materials, can solve the problems of inability to recycle, complex preparation process, easy to cause pollution, etc., and achieve the effects of small deformation shrinkage, simple processing technology, and good impact resistance effect.
- Summary
- Abstract
- Description
- Claims
- Application Information
AI Technical Summary
Problems solved by technology
Method used
Examples
preparation example Construction
[0020] The invention provides a technical solution: a resin protective film material and a preparation method thereof, comprising the following specific material parts, wherein 1-3 parts of phenolic resin, 3-5 parts of polystyrene, 1.2-2.5 parts of polyester resin, 3.5-9 parts of polyamide resin, 6-12 parts of polytetrafluoroethylene, 6-12 parts of polyvinylidene fluoride, 5-8 parts of polystyrene, 5-10 parts of polycarbonate, 7-14 parts of polypropylene, ring 2-5 parts of oxygen resin, 4-8 parts of polyphenylene sulfide, 2-6 parts of polyether ether ketone, 1.5-5 parts of polyamide, 1.2-3.5 parts of polyethersulfone, 3-5 parts of isoamyl methacrylate , 0.5-1.4 parts of dispersant, 0.7-1.5 parts of antioxidant, 0.8-1.6 parts of compatibilizer.
[0021] Also includes the following specific material parts, including 3 parts of phenolic resin, 5 parts of polystyrene, 2.5 parts of polyester resin, 9 parts of polyamide resin, 12 parts of polytetrafluoroethylene, 12 parts of polyvin...
Embodiment 1
[0034] 3 parts of phenolic resin, 5 parts of polystyrene, 2.5 parts of polyester resin, 9 parts of polyamide resin, 12 parts of polytetrafluoroethylene, 12 parts of polyvinylidene fluoride, 8 parts of polystyrene, 10 parts of polycarbonate, poly 14 parts of propylene, 5 parts of epoxy resin, 8 parts of polyphenylene sulfide, 6 parts of polyether ether ketone, 5 parts of polyamide, 3.5 parts of polyethersulfone, 5 parts of isoamyl methacrylate, 1.4 parts of dispersant, 1.5 parts of oxygen agent, 1.6 parts of compatibilizer.
[0035] Firstly, the organic raw materials are crushed separately, soaked in ethanol solution, washed with washing after soaking, and dried;
[0036] Then phenolic resin, polystyrene, polyester resin, polyamide resin, polytetrafluoroethylene, polyvinylidene fluoride, polystyrene, polycarbonate, polypropylene, epoxy resin, polyphenylene sulfide, polyether ether Feed ketone, polyamide, polyethersulfone, and isoamyl methacrylate into the mixing box, fully mix...
Embodiment 2
[0042]1 part of phenolic resin, 3 parts of polystyrene, 1.2 parts of polyester resin, 3.5 parts of polyamide resin, 6 parts of polytetrafluoroethylene, 6 parts of polyvinylidene fluoride, 5 parts of polystyrene, 5 parts of polycarbonate, poly 7 parts of propylene, 2 parts of epoxy resin, 4 parts of polyphenylene sulfide, 2 parts of polyether ether ketone, 1.5 parts of polyamide, 1.2 parts of polyethersulfone, 3 parts of isoamyl methacrylate, 0.5 parts of dispersant, anti 0.7 parts of oxygen agent, 0.8 parts of compatibilizer.
[0043] Firstly, the organic raw materials are crushed separately, soaked in ethanol solution, washed with washing after soaking, and dried;
[0044] Then phenolic resin, polystyrene, polyester resin, polyamide resin, polytetrafluoroethylene, polyvinylidene fluoride, polystyrene, polycarbonate, polypropylene, epoxy resin, polyphenylene sulfide, polyether ether Feed ketone, polyamide, polyethersulfone, and isoamyl methacrylate into the mixing box, fully ...
PUM
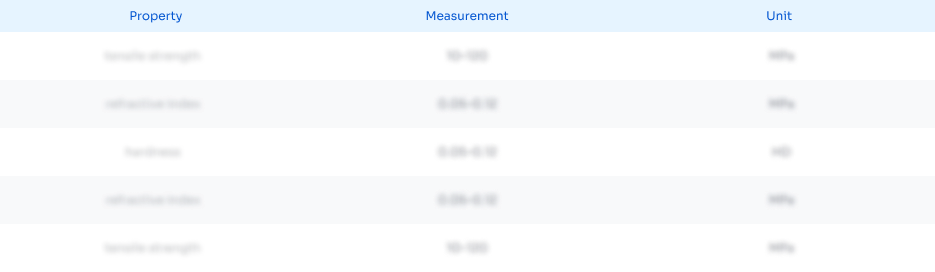
Abstract
Description
Claims
Application Information

- Generate Ideas
- Intellectual Property
- Life Sciences
- Materials
- Tech Scout
- Unparalleled Data Quality
- Higher Quality Content
- 60% Fewer Hallucinations
Browse by: Latest US Patents, China's latest patents, Technical Efficacy Thesaurus, Application Domain, Technology Topic, Popular Technical Reports.
© 2025 PatSnap. All rights reserved.Legal|Privacy policy|Modern Slavery Act Transparency Statement|Sitemap|About US| Contact US: help@patsnap.com