Zirconium oxide microspheres and preparation method thereof
A technology of zirconia microbeads and zirconia, applied in chemical instruments and methods, other chemical processes, etc., can solve the problems of poor quality and dimensional stability of zirconia microbeads, fragile beads, etc., to solve the risk of broken beads, size Consistent, simple process results
- Summary
- Abstract
- Description
- Claims
- Application Information
AI Technical Summary
Problems solved by technology
Method used
Examples
Embodiment 1
[0023] Example 1: The zirconia microbeads and its preparation method provided in this example, the zirconia microbeads are made of zirconia high-solid slurry and titration emulsion, which are heated and titrated, then settled and condensed into zirconia spheres, and then treated at low temperature Obtained after debinding and sintering, the mass ratio of the zirconia high-solid slurry to titrated emulsion is 4-6:4-6. Zirconia high solids slurry is made of the following components by weight: 80-100 parts of zirconia powder, 16-20 parts of deionized water, 1-3 parts of ammonium polyacrylate dispersant, 2 parts of acrylamide -3 parts, N, N-methylenebisacrylamide 0.2-0.4 parts; titrated emulsion is made of the following components in volume percentage: 60%-80% simethicone, 19%-39% propylene glycol, 1% Span 80; zirconia powder is made of the following components by weight: 100 parts of zirconia powder, 120-240 parts of deionized water, 2-4 parts of ammonium polyacrylate, 4-6 parts ...
Embodiment 2
[0027] Embodiment 2: The zirconia microbeads provided in this embodiment and the preparation method thereof are basically the same as in Embodiment 1, except that:
[0028] S1. Preparation of zirconia high-solid slurry: The total amount of ingredients is 100kg, using 80kg of zirconia powder, 16kg of deionized water, 2kg of ammonium polyacrylate dispersant, 1.8kg of acrylamide, and 0.2kg of NN-methylenebisacrylamide , mixed and placed in a roller mill for grinding at room temperature for 2 hours; the zirconia powder is made of the following components by weight: 100 parts of zirconia powder, 120 parts of deionized water, 2 parts Ammonium polyacrylate, 6 parts of cetyltrimethylammonium bromide, 8 parts of ethanol solution of silane coupling agent;
[0029] S2. Titration emulsion preparation: The titration emulsion is prepared according to the volume ratio of 60%% simethicone oil, 39% propylene glycol, and 1% Span 80, and mixed evenly; the mass ratio of the zirconia high-solid sl...
Embodiment 3
[0033] Example 3: The zirconia microspheres provided in this example and their preparation method are basically the same as those in Example 1 and Example 2, except that the zirconia microspheres are made of zirconia high-solids slurry and The titrated emulsion settles and coagulates into zirconia spheres after heating and titrating, and is obtained after low-temperature debinding and sintering. The mass ratio of the zirconia high-solid slurry to the titrated emulsion is 6:4. Zirconia high solids slurry is made of the following components by weight: 80 parts of zirconia powder, 20 parts of deionized water, 1 part of ammonium polyacrylate dispersant, 3 parts of acrylamide, N, N- 0.2 parts of methylenebisacrylamide; the titration emulsion is made of the following components in volume percentage: 80% simethicone, 19% propylene glycol, 1% Span 80; the zirconia powder is made of the following parts by weight Made of components: 100 parts of zirconia powder, 240 parts of deionized w...
PUM
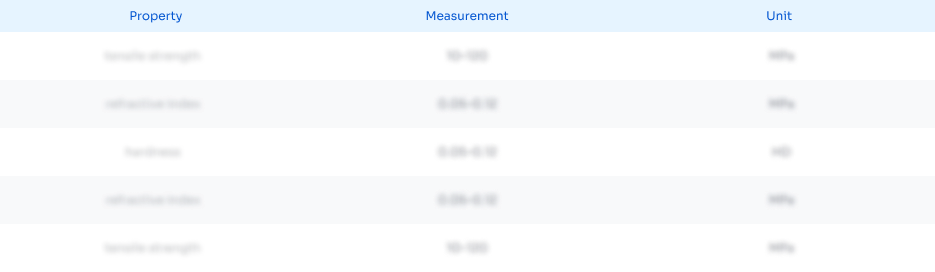
Abstract
Description
Claims
Application Information

- R&D
- Intellectual Property
- Life Sciences
- Materials
- Tech Scout
- Unparalleled Data Quality
- Higher Quality Content
- 60% Fewer Hallucinations
Browse by: Latest US Patents, China's latest patents, Technical Efficacy Thesaurus, Application Domain, Technology Topic, Popular Technical Reports.
© 2025 PatSnap. All rights reserved.Legal|Privacy policy|Modern Slavery Act Transparency Statement|Sitemap|About US| Contact US: help@patsnap.com