Trench manufacturing method
A manufacturing method and trench technology, applied in semiconductor/solid-state device manufacturing, electrical components, circuits, etc., can solve the problems of etching or etching stop, etching trench bridging defect photoresist residue, etc.
- Summary
- Abstract
- Description
- Claims
- Application Information
AI Technical Summary
Problems solved by technology
Method used
Image
Examples
Embodiment Construction
[0026] The groove manufacturing method proposed by the present invention will be further described in detail below in conjunction with the accompanying drawings and specific embodiments. Advantages and features of the present invention will be apparent from the following description and claims. It should be noted that all the drawings are in a very simplified form and use imprecise scales, and are only used to facilitate and clearly assist the purpose of illustrating the embodiments of the present invention.
[0027] A trench making method such as figure 1 Shown include:
[0028] A substrate is provided, the surface of the substrate is sequentially formed with a dielectric layer, an advanced graphics film layer, an anti-reflection coating layer and a patterned photoresist layer with a first opening;
[0029] Using the patterned photoresist layer as a mask, etching the antireflection coating layer to form a second opening, and stopping on the advanced graphics film layer, and...
PUM
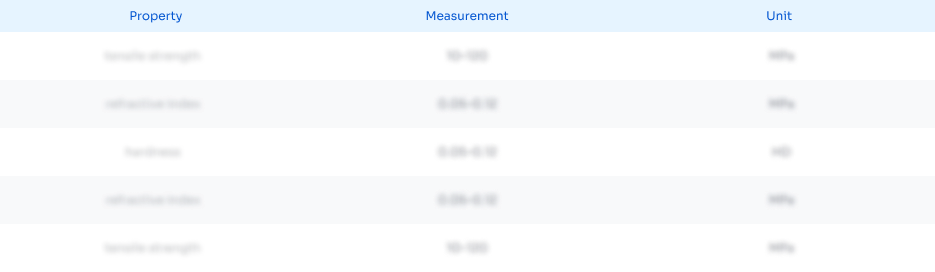
Abstract
Description
Claims
Application Information

- R&D
- Intellectual Property
- Life Sciences
- Materials
- Tech Scout
- Unparalleled Data Quality
- Higher Quality Content
- 60% Fewer Hallucinations
Browse by: Latest US Patents, China's latest patents, Technical Efficacy Thesaurus, Application Domain, Technology Topic, Popular Technical Reports.
© 2025 PatSnap. All rights reserved.Legal|Privacy policy|Modern Slavery Act Transparency Statement|Sitemap|About US| Contact US: help@patsnap.com