Heat treatment composite process and die steel obtained according to heat treatment composite process
A composite process and die steel technology, applied in metal material coating process, coating, solid-state diffusion coating, etc., can solve the problems of short service life of die-casting molds, uneven distribution of carbon and alloy components, etc., to improve toughness, improve Die melting resistance and thermal fatigue performance, the effect of improving thermal stability
- Summary
- Abstract
- Description
- Claims
- Application Information
AI Technical Summary
Problems solved by technology
Method used
Image
Examples
Embodiment 2
[0061] Example 2 and Example 7 adopt the process of tissue pretreatment + conventional quenching, and the service life of the two groups is 2000 and 2900 pieces respectively. It can be seen that compared with Example 1 and Example 6, the mold steel that has undergone tissue pretreatment is the same under other conditions. In this case, the life expectancy is greatly improved.
Embodiment 3
[0062] Example 3 and Example 8 adopt conventional quenching + place in a low temperature environment of -150°C for 15 hours for ultra-cryogenic treatment, and the service life of the two groups is 2500 and 2600 pieces respectively. H13 and 1.2344 die steel, under other conditions being the same, in the die steel structure of embodiment 4 and embodiment 9, the retained austenite AR (unit %) is 12 and 11 respectively, and the life after comparison is larger improve.
Embodiment 4
[0063] Example 4 and Example 9 adopt the metal treatment method of tissue pretreatment + conventional quenching + placing in a low temperature environment of -150°C for 15 hours for ultra-cryogenic treatment. Example 6, H13 and 1.2344 die steels placed in a low-temperature environment at -150°C for 15 hours for ultra-cryogenic treatment, under the same conditions, in the die steel structures of Examples 4 and 9, retained austenite AR (unit %) is 1.7 and 1.8 respectively, and the life expectancy after comparison is greatly improved.
PUM
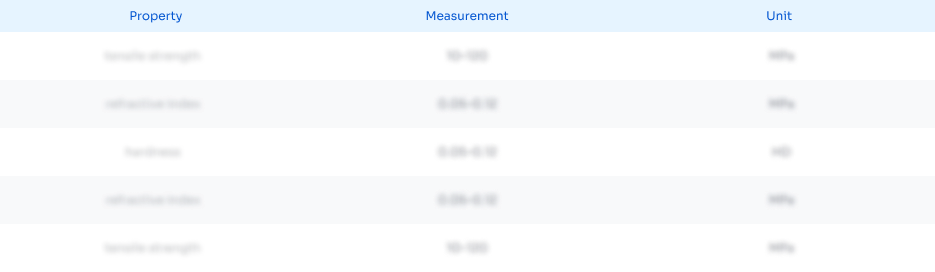
Abstract
Description
Claims
Application Information

- R&D Engineer
- R&D Manager
- IP Professional
- Industry Leading Data Capabilities
- Powerful AI technology
- Patent DNA Extraction
Browse by: Latest US Patents, China's latest patents, Technical Efficacy Thesaurus, Application Domain, Technology Topic, Popular Technical Reports.
© 2024 PatSnap. All rights reserved.Legal|Privacy policy|Modern Slavery Act Transparency Statement|Sitemap|About US| Contact US: help@patsnap.com