A Micro Friction Stir Welding Process for Electronic Packaging
A friction welding and electronic packaging technology, applied in welding equipment, non-electric welding equipment, manufacturing tools, etc., can solve the problems of high density and pollution-free effect, and achieve good application prospects, high processing efficiency, and improved mechanics. performance effect
- Summary
- Abstract
- Description
- Claims
- Application Information
AI Technical Summary
Problems solved by technology
Method used
Image
Examples
specific Embodiment approach 1
[0024] Specific implementation mode one: combine Figure 1~6 Describe this embodiment, a micro-stir friction welding process for electronic packaging. First, the first pad 1 and the second pad 2 to be welded are a group of pads. When the pads are arranged in a single point , the press-in hole 4 is prefabricated on the first substrate 3, and the pad group is arranged in parallel between the first substrate 3 and the second substrate 5, and the center position of the press-in hole 4 is aligned with the pad group Arrange in the center, then use the clamp to press the first substrate 3 and the second substrate 5, align the stirring head 6 coaxially above the pressing hole 4, control the stirring head 6 to rotate at a high speed and move down into the pressing hole 4, Then press it into the first pad 1, and realize the permanent metallurgical connection between the first pad 1 and the second pad 2 under the set press-in amount and holding time, and finally control the stirring head...
PUM
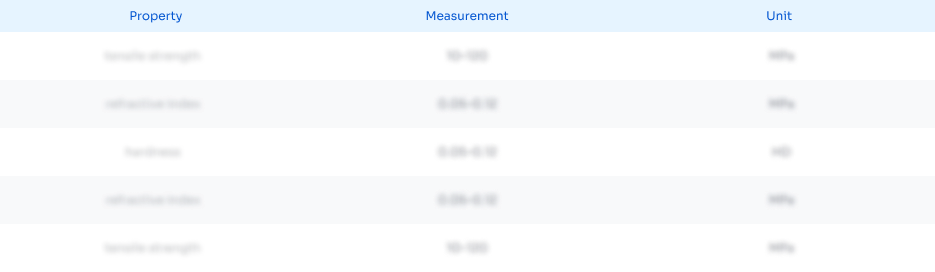
Abstract
Description
Claims
Application Information

- Generate Ideas
- Intellectual Property
- Life Sciences
- Materials
- Tech Scout
- Unparalleled Data Quality
- Higher Quality Content
- 60% Fewer Hallucinations
Browse by: Latest US Patents, China's latest patents, Technical Efficacy Thesaurus, Application Domain, Technology Topic, Popular Technical Reports.
© 2025 PatSnap. All rights reserved.Legal|Privacy policy|Modern Slavery Act Transparency Statement|Sitemap|About US| Contact US: help@patsnap.com