Aqueous acrylic water-resistant road marking coating and preparation method thereof
A water-based acrylic, road marking technology, used in anti-corrosion coatings, coatings, etc., can solve the problems of poor water resistance, uneven curing, reduced strength and toughness of the paint film, achieve fine and uniform film formation, improve safety and environmental protection performance, improved gloss retention
- Summary
- Abstract
- Description
- Claims
- Application Information
AI Technical Summary
Problems solved by technology
Method used
Image
Examples
Embodiment 1
[0031]Raw material composition (parts by weight): 100 parts of modified acrylic resin, 1 part of diacetone acrylamide, 1 part of dihydrazine adipate, 5 parts of neopentyl glycol, 10 parts of maleic anhydride, 3 parts of adipate , 10 parts of coalescent, 5 parts of glyceryl tristearate and 5 parts of defoamer BYK024. The film-forming aid is composed of the following raw materials in parts by weight: 12% of silane coupling agent, 15% of tea polyphenol, 43% of 800 mesh calcium powder, 15% of Tween-80, 10% of Span-80 and modified hydrogenated castor Sesame oil 5%.
[0032] The modified acrylic resin is prepared from the following raw materials by weight: 30 parts of methyl methacrylate, 10 parts of n-butyl acrylate, 15 parts of acrylic acid, 10 parts of hydroxyethyl acrylate, 20 parts of hydroxyethyl acrylate, and 25 parts of isocyanate , 10 parts of FEVE fluororesin, 5 parts of triethoxysilane, 50 parts of glycidyl tertiary carbonate and 1 part of potassium persulfate.
[0033]...
Embodiment 2
[0039] Composition of raw materials (parts by weight): 200 parts of modified acrylic resin, 3 parts of diacetone acrylamide, 3 parts of dihydrazine adipate, 10 parts of neopentyl glycol, 15 parts of maleic anhydride, 7 parts of adipate , 20 parts of film-forming aid, 10 parts of dispersant CT-13610 parts and 10 parts of silicone defoamer. The film-forming aid is made up of the following raw materials by weight: 12% of silane coupling agent, 15% of antioxidant 1010, 43% of 800 mesh calcium powder, 15% of Tween-80, 10% of Span-80 and anti-settling agent BYK-430 5%.
[0040] The modified acrylic resin is prepared from the following raw materials by weight: 50 parts of methyl methacrylate, 30 parts of n-butyl acrylate, 35 parts of acrylic acid, 50 parts of hydroxyethyl acrylate, 55 parts of isocyanate, 30 parts of FEVE fluororesin, 10 parts of triethoxysilane, 100 parts of glycidyl tert-carbonate and 2 parts of tert-butyl hydroperoxide.
[0041] Modified acrylic resins are prepa...
Embodiment 3
[0046] Composition of raw materials (parts by weight): 130 parts of modified acrylic resin, 2 parts of diacetone acrylamide, 1 part of dihydrazine adipate, 6 parts of neopentyl glycol, 8 parts of maleic anhydride, 4 parts of adipate , 12 parts of film-forming aid, 6 parts of sodium acrylic acid copolymer and 6 parts of GPE type defoamer. The film-forming aid is composed of the following raw materials in parts by weight: 12% of silane coupling agent, 15% of tea polyphenols, 43% of 800 mesh calcium powder, 15% of Tween-8010%, 10% of Span-8010% and 5% of modified hydrogenated castor oil %.
[0047] The modified acrylic resin is prepared from the following raw materials by weight: 35 parts of methyl methacrylate, 15 parts of n-butyl acrylate, 17 parts of acrylic acid, 20 parts of hydroxyethyl acrylate, 25 parts of isocyanate, 15 parts of FEVE fluororesin, 6 parts of triethoxysilane, 60 parts of glycidyl tertiary carbonate and 1.2 parts of potassium persulfate.
[0048] Modified ...
PUM
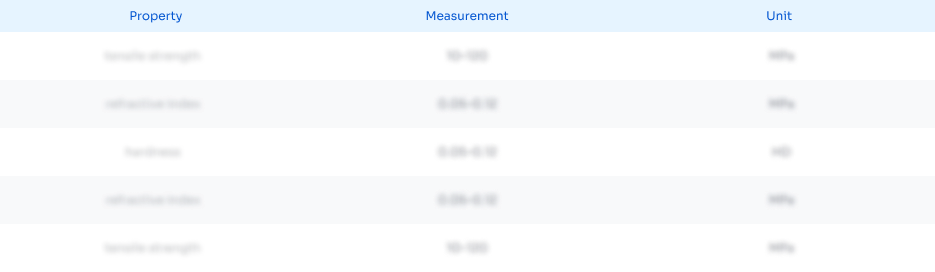
Abstract
Description
Claims
Application Information

- R&D
- Intellectual Property
- Life Sciences
- Materials
- Tech Scout
- Unparalleled Data Quality
- Higher Quality Content
- 60% Fewer Hallucinations
Browse by: Latest US Patents, China's latest patents, Technical Efficacy Thesaurus, Application Domain, Technology Topic, Popular Technical Reports.
© 2025 PatSnap. All rights reserved.Legal|Privacy policy|Modern Slavery Act Transparency Statement|Sitemap|About US| Contact US: help@patsnap.com