Method for preparing glycine by utilizing common ion effect
A technology of the same ion effect and glycine, which is applied in the field of clean production technology of glycine, can solve the problems of large energy consumption, cannot be recycled, and low catalytic ability of urotropine, so as to improve the yield and product quality, and reduce by-products. the resulting effect of
- Summary
- Abstract
- Description
- Claims
- Application Information
AI Technical Summary
Problems solved by technology
Method used
Examples
Embodiment 1
[0056] In 2000 liters of glycine synthetic enamel reaction kettle equipped with stirring, heating and circulating water cooling, add 1600 liters of alcohol-water mixed solvent with 70% methanol content, 3 kilograms of catalyst 4-dimethylaminopyridine, 305 kilograms of ammonium chloroacetate, and heat up When the temperature reaches 50°C, the ammonia flow reaction starts, and the temperature is controlled between 55°C and 65°C. When the pH value of the solution reaches 7.0, the ammonia flow is stopped, and the reaction is kept for 30 minutes. Glycine was separated by centrifugation at 55°C, washed with methanol and dried to obtain 175.8 kg of glycine with a glycine content of 98.8% and a chloride ion content of 0.35.
[0057] The centrifuged liquid (mixed solvent for circulating reaction) was sent to the crystallization kettle, and 305 kg of solid ammonium chloroacetate was added, and the temperature was slowly lowered to 10°C. After centrifugation and drying, 65.8 kg of ammoniu...
Embodiment 2
[0059] Take the centrifugate in Example 1, send it to the glycine synthesis kettle, raise the temperature to 50°C, start the ammonia reaction, control the temperature between 55°C-65°C, stop the ammonia flow when the pH value of the solution reaches 7.2 , keep warm for 30 minutes. Glycine was separated by centrifugation at 55°C, washed with methanol and dried to obtain 194.75 kg of glycine with a glycine content of 98.7% and a chloride ion content of 0.39. The yield of glycine is 95.1%.
[0060] The centrifuged liquid (mixed solvent for circulating reaction) was sent to the crystallization kettle, and 305 kg of solid ammonium chloroacetate was added, and the temperature was slowly lowered to 10°C. After centrifugation and drying, 141.2 kg of ammonium chloride was obtained.
Embodiment 3
[0062] Add 1600 liters of alcohol-water mixed solvent with a methanol content of 70%, 104 kg of urotropine, and 305 kg of ammonium chloroacetate in a 2,000-liter glycine synthesis enamel reaction kettle equipped with stirring, heating, and circulating water cooling, and heat up to 50°C , start the ammonia reaction, the temperature is controlled between 55°C-65°C, when the pH value of the solution reaches 7.0, stop the ammonia flow, and keep warm for 30 minutes. Glycine was separated by centrifugation at 55°C, washed with methanol and dried to obtain 168.8 kg of glycine with a glycine content of 98.9% and a chloride ion content of 0.36.
[0063] The centrifuged liquid (mixed solvent for circulating reaction) was sent to the crystallization kettle, and 305 kg of solid ammonium chloroacetate was added, and the temperature was slowly lowered to 10°C. After centrifugation and drying, 63.1 kg of ammonium chloride was obtained.
PUM
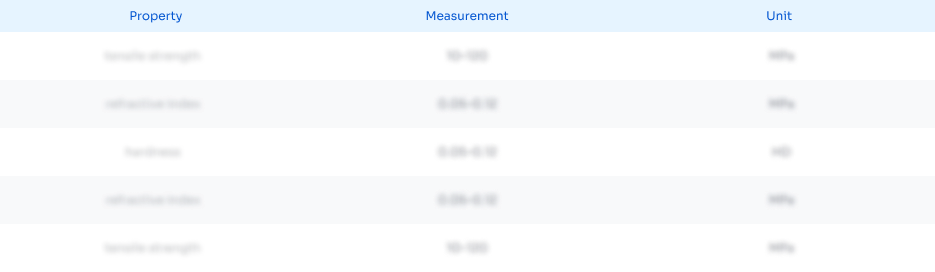
Abstract
Description
Claims
Application Information

- Generate Ideas
- Intellectual Property
- Life Sciences
- Materials
- Tech Scout
- Unparalleled Data Quality
- Higher Quality Content
- 60% Fewer Hallucinations
Browse by: Latest US Patents, China's latest patents, Technical Efficacy Thesaurus, Application Domain, Technology Topic, Popular Technical Reports.
© 2025 PatSnap. All rights reserved.Legal|Privacy policy|Modern Slavery Act Transparency Statement|Sitemap|About US| Contact US: help@patsnap.com