A method for preparing high-performance powder metallurgy titanium and titanium alloy products by solid phase deoxidation
A powder metallurgy and high-performance technology, applied in the field of powder metallurgy titanium, can solve the problems of reducing sintering density, strength and elongation, expensive rare earth elements, and high cost of purifying agents, achieving excellent comprehensive mechanical properties, reducing adverse effects, Effect of improving sintering activity
- Summary
- Abstract
- Description
- Claims
- Application Information
AI Technical Summary
Problems solved by technology
Method used
Examples
Embodiment 1
[0020] According to the mass percentage, it is composed of the following ingredients: 4wt.%TiCl 2 , the balance is hydrodehydrogenation pure titanium powder (HDH-Ti), wherein the particle size of HDH-Ti is D 50 =15 μm, the oxygen content is 3500 ppm. Concrete preparation steps are as follows:
[0021] (1) TiCl that meets the formula requirements 2 Mix with HDH-Ti under the protection of argon atmosphere in the glove box, and mix on a mixer for 15 hours to obtain a uniform mixed powder;
[0022] (2) Put the mixed powder into a cold isostatic silica gel bag in an argon-protected glove box and vibrate, vacuumize and seal it, and carry out cold isostatic pressing at a pressing pressure of 300 MPa, and hold the pressure for 2 minutes to obtain a compact sample;
[0023] (3) Put the compact sample into the sintering furnace for vacuum sintering, the vacuum degree is 10 -3 Pa, first heat preservation at 600°C for 60min, and then heat preservation at 1170°C for 1h, and finally ob...
Embodiment 2
[0025] According to the mass percentage, it is composed of the following ingredients: 3wt.%TiCl 2 , the balance is HDH-TC4 titanium alloy powder, wherein the particle size of HDH-TC4 is D 50 =30 μm, the oxygen content is 2500 ppm. Concrete preparation steps are as follows:
[0026] (1) TiCl that meets the formula requirements 2 Mix with HDH-TC4 under the protection of argon atmosphere in the glove box, and mix on the mixer for 10 hours to obtain a uniform mixed powder;
[0027] (2) Put the mixed powder into a cold isostatic pressing rubber sheath in an argon-protected glove box and vibrate, vacuumize and seal it, and carry out cold isostatic pressing at a pressing pressure of 400 MPa and hold the pressure for 1 min to obtain a green compact sample;
[0028] (3) Put the compacted sample into a sintering furnace for argon sintering, first hold it at 750°C for 90 minutes, then hold it at 1250°C for 1.5h, and finally obtain high-performance TC4 titanium alloy parts.
PUM
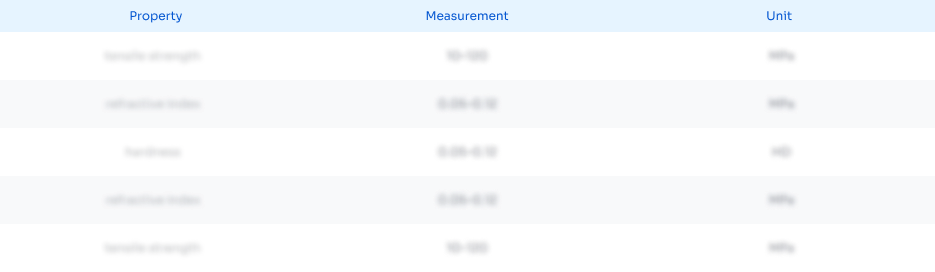
Abstract
Description
Claims
Application Information

- Generate Ideas
- Intellectual Property
- Life Sciences
- Materials
- Tech Scout
- Unparalleled Data Quality
- Higher Quality Content
- 60% Fewer Hallucinations
Browse by: Latest US Patents, China's latest patents, Technical Efficacy Thesaurus, Application Domain, Technology Topic, Popular Technical Reports.
© 2025 PatSnap. All rights reserved.Legal|Privacy policy|Modern Slavery Act Transparency Statement|Sitemap|About US| Contact US: help@patsnap.com