Large-specification fine-grain high-strength anti-seismic reinforcement steel bars and preparation method thereof
An anti-seismic steel bar and high-strength technology is applied in the field of large-scale fine-grained and high-strength seismic-resistant steel bars and their preparation. The effect of improving corrosion resistance and improving seismic performance
- Summary
- Abstract
- Description
- Claims
- Application Information
AI Technical Summary
Problems solved by technology
Method used
Image
Examples
preparation example Construction
[0047] The invention also provides a preparation method of Φ28-36mm HRB600 high-strength seismic steel bars for hydropower station engineering, which specifically includes the following steps:
[0048] A. Molten steel smelting: the chemical composition C 4.0-5.0wt%, Si 0.30-0.55wt%, Mn 0.30-0.60wt%, P0.080-0.120wt%, S≤0.045wt%, the rest is Fe and unavoidable Impurity molten iron, chemical composition C 0.12-0.20wt%, Si 0.15-0.35 wt%, Mn 0.35-0.65wt%, P 0.025-0.040wt%, S 0.025-0.040wt%, the rest is Fe and unavoidable Impurity scrap steel and chemical composition C 3.0-3.5wt%, Si 0.30-0.55wt%, Mn0.40-0.65wt%, P 0.060-0.100wt%, S 0.030-0.050wt%, the rest is Fe and unavoidable The impurity pig iron is 930-940kg / t steel , 100-115kg / t steel , 30-40kg / t steel It is added to a 120-ton converter for conventional top-bottom composite blowing, and lime, dolomite, and magnesite balls are added in the conventional amount to make slag. The end-point carbon content is controlled to 0.08-0.12wt%...
Embodiment 1
[0057] This embodiment provides a Φ28mm large-size HRB600 high-strength seismic steel bar for hydropower station engineering, which is prepared through the following process steps:
[0058] A. Molten steel smelting: the chemical composition C 4.0wt%, Si 0.30wt%, Mn 0.30wt%, P 0.080wt%, S0.020wt%, the rest is Fe and unavoidable impurities of molten iron, chemical composition C 0.12 wt%, Si 0.15wt%, Mn0.35wt%, P 0.025wt%, S 0.025wt%, the rest is Fe and not t steel Avoidable impurities of steel scrap and chemical composition C3.0wt%, Si 0.30wt%, Mn 0.40wt%, P 0.060wt%, S 0.030wt%, the rest are Fe and unavoidable impurities of pig iron respectively 930kg / , 100kg / t steel , 30kg / t steel It is added to a 120-ton converter for conventional top-bottom composite blowing, lime, dolomite, and magnesite balls are added to make slag according to the conventional amount. The end-point carbon content is controlled to 0.08wt%, and the tapping temperature is 1640°C; the bottom of the ladle before t...
Embodiment 2
[0069] This embodiment 2 provides a Φ32mm large-size HRB600 high-strength seismic steel bar used in hydropower stations, which is prepared through the following process steps:
[0070] A. Molten steel smelting: the chemical composition C 4.5wt%, Si 0.42wt%, Mn 0.45wt%, P 0.100wt%, S0.035wt%, the rest is Fe and unavoidable impurities of molten iron, chemical composition C 0.16 wt%, Si 0.25 wt%, Mn0.50wt%, P 0.032wt%, S 0.032wt%, the rest is scrap steel with Fe and unavoidable impurities and chemical composition C3.2wt%, Si 0.42 wt%, Mn 0.52 wt%, P 0.080wt%, S 0.040wt%, the rest is Fe and unavoidable impurities of pig iron at 935kg / t steel , 110kg / t steel , 35kg / t steel It is added to a 120-ton converter for conventional top-bottom composite blowing, lime, dolomite, and magnesite balls are added in the conventional amount to make slag. The end-point carbon content is controlled to 0.10wt% and the tapping temperature is 1655℃; before tapping, it faces the bottom of the ladle. Add li...
PUM
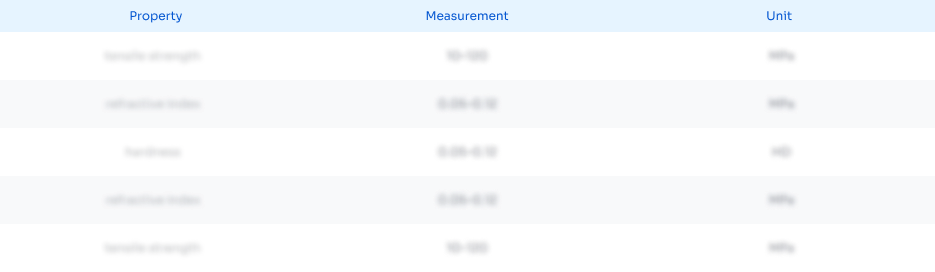
Abstract
Description
Claims
Application Information

- R&D
- Intellectual Property
- Life Sciences
- Materials
- Tech Scout
- Unparalleled Data Quality
- Higher Quality Content
- 60% Fewer Hallucinations
Browse by: Latest US Patents, China's latest patents, Technical Efficacy Thesaurus, Application Domain, Technology Topic, Popular Technical Reports.
© 2025 PatSnap. All rights reserved.Legal|Privacy policy|Modern Slavery Act Transparency Statement|Sitemap|About US| Contact US: help@patsnap.com