Treatment method of maleic anhydride production waste liquid
A treatment method and technology for waste liquid, applied in combustion methods, chemical instruments and methods, heating water/sewage treatment, etc., can solve the problems of large fuel gas consumption, low B/C ratio, uneconomical, etc., and reduce production and operation. Cost, lower operating temperature, less coking effect
- Summary
- Abstract
- Description
- Claims
- Application Information
AI Technical Summary
Problems solved by technology
Method used
Image
Examples
Embodiment 1
[0024] See the following table for the waste liquid indicators of the maleic anhydride plant:
[0025] Table 1 Waste liquid index of maleic anhydride plant
[0026]
[0027] The waste liquid enters the preheater through the feed pump, the feed rate is 10000kg / h, the first-effect evaporator is heated by 4500kg / h steam, the steam pressure is 0.3MPa, and the gas phase outlet pressure of the three-effect evaporator is controlled to 12KPaA. At this time, the first-effect evaporator The gas phase temperature is 96°C, the bottom liquid phase temperature is 108°C, the gas phase temperature of the second-effect evaporator is 65°C, the bottom liquid phase temperature is 86°C, the gas phase temperature of the three-effect evaporator is 50°C, the bottom liquid phase temperature is 68°C, and the bottom of the three-effect evaporator is concentrated Liquid output 1000kg / h. The maleic anhydride plant is equipped with a direct-fired incinerator, and the concentrated liquid is sent to the ...
Embodiment 2
[0029] The indicators of the waste liquid are the same as in Example 1, the waste liquid enters the preheater through the feed pump, the feed rate is 10000kg / h, the first effect evaporator is heated by 4500kg / h steam, the steam pressure is 0.5MPa, and the gas phase outlet pressure of the three effect evaporator is controlled 20KPaA, at this time, the gas phase temperature of the first effect evaporator is 106°C, the bottom liquid phase temperature is 118°C, the gas phase temperature of the second effect evaporator is 75°C, the bottom liquid phase temperature is 96°C, the gas phase temperature of the three effect evaporator is 60°C, and the bottom liquid phase temperature is 77 ℃, the discharge of concentrated liquid at the bottom of the three-effect evaporator is 1000kg / h. The maleic anhydride plant is equipped with a direct-fired incinerator, and the concentrated liquid is sent to the direct-fired incinerator for treatment. Using butane gas as fuel, controlling the furnace te...
Embodiment 3
[0031] The indicators of the waste liquid are the same as in Example 1, the waste liquid enters the preheater through the feed pump, the feed rate is 10000kg / h, the first effect evaporator is heated by 3000kg / h steam, the steam pressure is 0.3MPa, and the gas phase outlet pressure of the three effect evaporator is controlled 12KPaA, at this time, the gas phase temperature of the first effect evaporator is 94 °C, the bottom liquid phase temperature is 103 °C, the gas phase temperature of the second effect evaporator is 66 °C, the bottom liquid phase temperature is 81 °C, the gas phase temperature of the three effect evaporator is 51 °C, and the bottom liquid phase temperature is 63 ℃, the discharge of concentrated liquid at the bottom of the three-effect evaporator is 4000kg / h. The maleic anhydride plant is equipped with a direct-fired incinerator, and the concentrated liquid is sent to the direct-fired incinerator for treatment. Use butane gas as fuel, control the furnace temp...
PUM
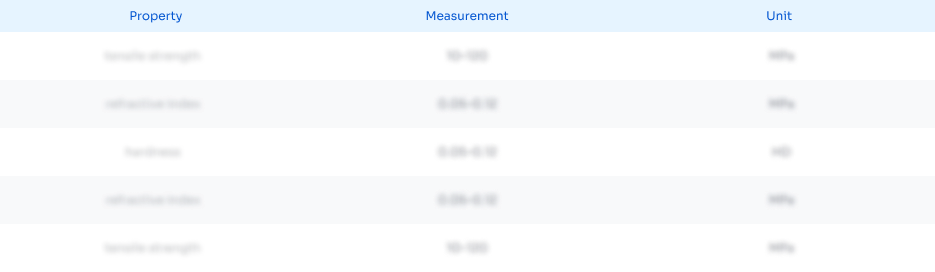
Abstract
Description
Claims
Application Information

- R&D
- Intellectual Property
- Life Sciences
- Materials
- Tech Scout
- Unparalleled Data Quality
- Higher Quality Content
- 60% Fewer Hallucinations
Browse by: Latest US Patents, China's latest patents, Technical Efficacy Thesaurus, Application Domain, Technology Topic, Popular Technical Reports.
© 2025 PatSnap. All rights reserved.Legal|Privacy policy|Modern Slavery Act Transparency Statement|Sitemap|About US| Contact US: help@patsnap.com